Biological organic fertilizer production line equipment, the main organic fertilizer raw materials to chicken manure, pig manure, cow manure, sheep manure, grass char, sludge, lignite, straw after fermentation mainly, can also be used to produce mixed feed granulation corn meal, bean powder, grass meal, etc.
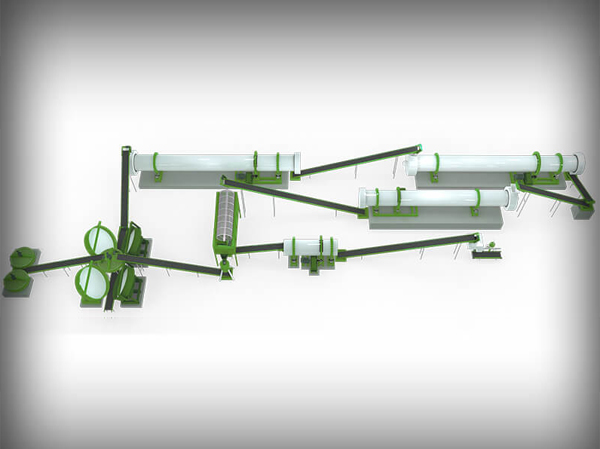
Automatic bio-organic fertilizer production line
processing capacity:1-100T/h
Application scope:animal manure, domestic waste, dead leaves, biogas residue, waste bacteria, etc into fertilizer
The complete set of equipment for the production line of bio organic fertilizer mainly consists of a turning machine, an organic fertilizer crusher, a dynamic batching machine, an organic fertilizer mixer, an organic fertilizer granulator, a dryer, a cooling machine, a drum screening machine, a coating machine, and an automatic packaging machine. Secondly, the more complex production process of organic fertilizer granules is as follows: the organic fertilizer raw materials (animal manure, household waste, dead branches and leaves, biogas residue, waste bacterial strains, etc.) are fermented and then enter a semi (high) humidity material crusher for crushing. Then, nitrogen, phosphorus, potassium and other elements (pure nitrogen, phosphorus pentoxide, potassium chloride, ammonium chloride, etc.) are added to make the mineral elements meet the required standards, and then stirred by a mixer before entering the granulation mechanism for granules. After coming out, they are dried, screened by a screening machine, and qualified products are packaged. Unqualified products are returned to the granulator for granulation.

Small bio-organic fertilizer production line is characterized by less investment and quick results, which is very suitable for customers who intend to invest in small fertilizer production plants. The price of small bio-organic fertilizer production line equipment is $20-50,000, the annual output of 20,000 tons of bio-organic fertilizer production line equipment is $6-100,000, and the annual output of 30,000 tons of bio-organic fertilizer production line equipment is $120-300,000. Different equipment material process requirements and the choice of different equipment (such as pelletizer, can use roller extrusion pelletizer, disk pelletizer, churn pelletizer, etc.) is an important factor affecting the price of the complete organic fertilizer production line.
Bio-organic fertilizer production line processing technology
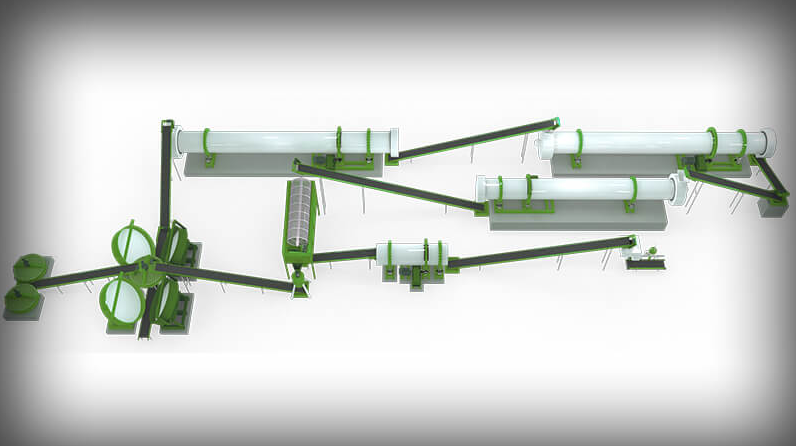
The fermentation system consists of a feed conveyor, a biological deodorization machine, a mixing mixer, a proprietary lifting and flipping machine, and an electrical automatic control system; The main equipment of the drying system includes belt conveyors, rotary dryers, coolers, induced draft fans, hot air stoves, etc; The deodorization and dust removal system consists of a settling chamber, a dust removal chamber, etc. Zhengzhou Tianci provides free drawings and guides users to build it for free;
Phase 2: Crushing batching mixing system
The crushing system includes new semi wet material crushers from Tianci Heavy Industry, LP chain crushers or cage crushers, belt conveyors, etc; The batching system includes equipment such as electronic batching system, disc feeder, vibrating screen, and can be configured with 6-8 types of raw materials at once; The mixing system consists of optional horizontal or disc mixers, vibrating screens, mobile belt conveyors, etc;
Phase 3: Granulation System
The granulation system requires the use of granulation equipment, and the available granulation equipment includes: compound fertilizer roller extrusion granulator, disc granulator, flat film granulator, bio organic fertilizer spherical granulator, organic fertilizer special granulator, rotary drum granulator, round throwing machine, compound fertilizer special granulator, etc;
Stage 4: Screening Drying/Cooling Packaging
The screening system is mainly completed by a drum screening machine, which can be equipped with screening machines and secondary screening machines to achieve high yield and good particle quality; The newly made granules have a relatively high moisture content and need to be dried to below 20% of the organic fertilizer standard. The dried granules of organic fertilizer are cooled by a cooling machine and then directly packaged.
Project conditions: Take the annual output of 10,000 tons as an example (2 to 3 tons per hour) biological organic fertilizer production line equipment configuration
Main raw materials: feces of livestock and poultry such as cattle, sheep, pigs, chickens, etc., unknown auxiliary materials (auxiliary materials include waste such as peat, sawdust, straw, soybean cake, and keratin powder, and the supply of surrounding materials shall not be less than 50 tons/day);
Production capacity: Annual output of 10000 tons (20 tons of livestock and poultry manure per day, 40 tons of auxiliary materials, calculated based on 300 days per year, 60 × 300=18000 tons, moisture ratio of 20%, maximum output of about 15000 tons), with an hourly output of 2 to 3 tons/hour (based on a conventional organic fertilizer factory production time of 12 hours per day, 300 days per year).
Factory personnel: produce approximately 1800 square meters; Fermentation workshop covers an area of approximately 1400 square meters; Approximately 6-10 people.
Name | Model number | Power (kw) | Quantity | Equipment use |
---|---|---|---|---|
Hydraulic tipping machine | ZPY-4 | Main motor 11*2, walking motor 2.2, shift motor 1.5, hydraulic pump motor 4 | 1 | Fermentation of organic fertilizer |
Forklift into the bin | TC-2*3 | Conveying motor 3 (variable frequency speed regulation), mixing motor 3 (variable frequency speed regulation) | 1 | Production feeding equipment, suitable for 30 forklifts |
Vertical mill | ZP-60 | 15 | 1 | The raw material of organic fertilizer is broken to meet the requirements of granulation |
Drum screen | GT – 1.2 * 4 | 5.5 | 1 | Fine screening of powdered raw materials after grinding |
Double shaft mixer | TC-40 | 15 | 1 | Stir raw materials and adjust granulation water |
Flat mold granulator | KP-40 | 30 | 1 | The main granulation equipment, processing powdery materials into columnar particles. |
Tumble dryer | HG – 1.2 | 7.5 | 1 | The finished particles are dried so that the moisture meets the storage requirements. |
Roller cooler | LQ – 1.0 | 5.5 | 1 | Cool the dried finished product particles to the appropriate temperature to prevent the finished product packaging from returning to moisture. |
Drum screen | GT – 1.2 * 4 | 5.5 | 1 | Finished particle sieving |
Packaging machine | Type 50 | 2.2 | Packaged finished products, ranging from 20kg to 50kg/ bag | |
Belt conveyor | B50 | 2.2~5kw | The devices are connected, and the power is equipped according to the length |