Detailed description of the biodegradable granulation machine: The barrel and screw of the parallel twin-screw extruder are designed and manufactured using the building block principle. According to the requirements of the processing material system and process formula, the aspect ratio, barrel structure, screw arrangement, mesh changing structure, exhaust quantity and position, feeding method, electrical control method, etc. can all be optimized and reasonably configured. Realize multifunctionality and versatility to adapt to the processing of polymer materials.
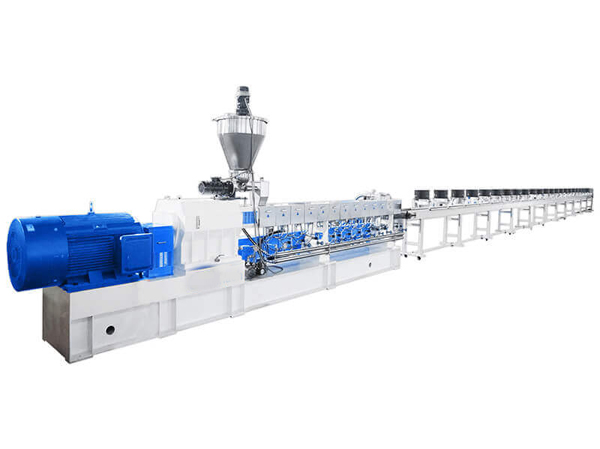
Manufacturer of automatic biodegradable granulation making machine
1) Biodegradable functional masterbatch
Biodegradable functional masterbatch can be compounded with any plastic such as PE/PET/PP to accelerate the molecular and chemical degradation of plastics, thereby helping to solve the problem of massive accumulation of plastic waste.
2) Biodegradable plastics: PPC、PABT、PLA、PBS、PCL、TPS、PVA、PVOH
Biodegradable plastics: PPC、PABT、PLA、PBS、PCL、TPS、PVA、PVOH
a) Melting PBAT and blending with PLA or PPC
The molten PBAT material with a temperature of 240 ℃ is pumped into a twin-screw extruder through a melt pump, and PLA or PPC pellets and chain extenders are added to the extruder through weight loss feeding. This is direct blending, which can save 40% of energy and provide better dispersibility compared to blending PBAT particles with PLA or PPC
Long L/D is required to react
Need for underwater granulation system to achieve high yield and automatic processing
Need a vacuum packaging system
b) PLA/PBS blend with starch powder
Pre mix with long L/D to achieve better dispersion effect
Specialized anti bridging feeding device
PLA substrate air-cooled die cutting, PBS substrate air-cooled drawing granulation
Need a vacuum packaging system
c) Composite of PVA and Starch
Two stage mixer for premixed reactions
Specialized anti bridging feeding device
The air-cooled die cutting system requires a water-cooled jacket for the die head
Need a vacuum packaging system
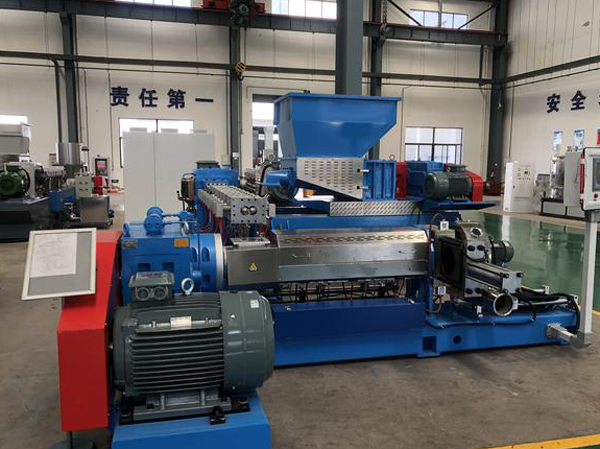
The principle of PLA degradation masterbatch granulator is to melt and granulate PLA raw materials to produce degradation masterbatch.
The process mainly includes melting, stirring, dispersion, filtration, granulation and other steps.
The key characteristics and advantages of PLA degradation masterbatch granulator will be analyzed in depth below.
- Efficient energy consumption:
The PLA degradation masterbatch granulator adopts advanced melt granulation technology, which can efficiently melt and uniformly stir PLA raw materials, improve production capacity and energy utilization efficiency. Compared to traditional granulation equipment, it has lower energy consumption and provides strong support for environmentally friendly production.
- Superior degradation performance:
PLA, as a biodegradable material, has excellent degradation performance and can rapidly decompose into carbon dioxide and water under specific conditions.
The PLA degradation masterbatch granulator can maintain the degradation performance of the material during the manufacturing process of PLA degradation masterbatch, ensuring that the produced masterbatch can be effectively degraded and reducing environmental pollution.
- Precise control:
The PLA degradation masterbatch granulator is equipped with an advanced control system that can monitor and adjust parameters such as melting temperature and granulation speed in real time to ensure product quality and consistency.
Through precise control, losses and waste in the production process can be reduced, and resource utilization efficiency can be improved.
- Strong flexibility:
The PLA degradation masterbatch granulator can adapt to different specifications and requirements of PLA raw materials, and can achieve customized production.
By adjusting equipment parameters and formulas, masterbatch with different particle sizes, colors, and degradation rates can be prepared to meet the diversity of market demand.
- High production efficiency:
The PLA degradation masterbatch granulator adopts an automated production mode, which is easy to operate and has high production efficiency.
By increasing the degree of automation and reducing human intervention, production costs can be reduced, production efficiency can be improved, and more sustainable development can be achieved.