The automatic disposable plastic cup & bowl making machine consists of a feeding rack, a heating box, a forming table, a receiving rack, an air compressor, etc. The main suitable materials are PP, PS, PET, PVC, HIPS, PE, etc. The long-term use temperature is 0-70 ℃.
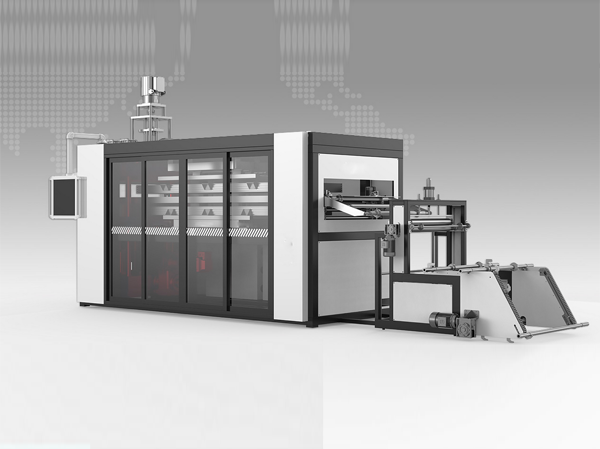
Manufacturer of automatic disposable plastic cup & bowl making machine
the main machine is a 4-guide pillar structure. the guide pillar material is 40Cr steel quenched and tempered, hard chrome plated on the outside, good rigidity, accurate guiding performance, wear resistance, and is helpful for the service life of the die shear;
automatic temperature control and adjustment of the heater, single-phase voltage regulating module non-contact output, stability, high precision, temperature control error ± 1 ℃. The upper and lower 8 zones, the electric furnace mouth to the mold direction forward, to achieve seamless connection between the mold and the electric furnace. The connecting part of the upper electric furnace and the mold is adjustable by adding a zone to reduce the temperature difference between the front and back rows of the product;
The sheet feeding chain adopts toothed double-row roller chain, the chain rail has a cooling water path, high cooling efficiency, and water saving. The inner cover stainless steel plate and the guide chain rail adopt 40Cr quenching, high working surface hardness and long service life;
feeding power adopts frequency conversion motor, hard tooth surface Taiwan brand reducer, high control precision, accurate positioning, start and stop response quickly;
is equipped with an automatic scrap winding device for leftover materials, with a maximum winding diameter of 1000mmm and easy winding change.;

(Model number) | TZF-730 | TZF-850 |
maximum mould size (Maximum mould size) | 750*450(mm) | 850*600(mm) |
maximum forming depth (Maximum moulding depth) | ≤180(mm) | 180(mm) |
sheet thickness (Sheet thickness) | 0.3~2.2(mm) | 0.3~1.8(mm) |
maximum forming speed (Maximum moulding speed) | 30times/minute | 30times/minute |
air pressure (Air pressure) | 0.6~0.8(Mpa) | 0.69~0.8(Mpa) |
air consumption (Air consumption) | 3.0m³/min | 3.0m³/min |
maximum sheet width (Maximum sheet width) | 760(mm) | 760(mm) |
applicable sheet (Applicable sheet) | PET,PP,PS,HIPS,PVC,PLA …. | PET,PP,PS,HIPS,PVC,PLA …. |
power supply | 380V,50Hz | 380V,50Hz |
Rated power | 180(kw) | 150(kw) |
used power | 80(kw) | 70(kw) |
device size (Equipment size) | 6200mm*1800mm*3200mm(L*W*H) | 5200mm*1600mm*2500mm(L*W*H) |
machine | ≈8(Tonnes) | ≈8(Tonnes) |
Analysis of Production Points for Plastic Cup Manufacturing Machine
Plastic cups are an indispensable part of our daily lives, integrated into various environments from homes to restaurants. Behind the scenes, the manufacturing process of these seemingly ordinary items involves complex machinery and intricate craftsmanship.
- Selection of disposable cup making machine
The core of plastic cup production is the machine that shapes and molds raw materials into the final product. Choosing a suitable disposable cup making machine is crucial, taking into account factors such as machine size, heating method, molding capacity, and automation function. The choice of machinery directly affects production efficiency, product quality, and overall operational efficiency.
- Material selection
The quality and characteristics of plastic cups depend on the selection of suitable raw materials for thermoforming. Common materials include polystyrene (PS), polyethylene terephthalate (PET), and polypropylene (PP), each with different characteristics such as transparency, rigidity, and heat resistance. The compatibility between materials and hot forming processes, as well as compliance with safety and regulatory standards, are crucial considerations.
- Process optimization
Optimizing the hot forming process is crucial for achieving consistent product quality and maximizing operational efficiency. This requires fine-tuning of parameters such as heating temperature, heating time, vacuum pressure, and cooling rate to ensure precise shaping and trimming of the cup. Implementing advanced control systems and monitoring tools can achieve real-time adjustments and minimize production changes to the greatest extent possible.
- Quality assurance
Maintaining strict quality assurance measures is crucial for providing plastic cups that meet customer expectations and regulatory requirements. From material inspection and process validation to product testing and validation, every stage of production undergoes rigorous review. Key quality parameters such as dimensional accuracy, wall thickness uniformity, and surface smoothness are closely monitored to ensure compliance with specifications.
- Equipment maintenance
Ensuring the reliability and service life of disposable cup thermoforming machines requires proactive maintenance and upkeep. Regular inspection, cleaning, lubrication, and replacement of worn parts are essential preventive measures. Timely troubleshooting and maintenance of equipment can minimize downtime and maintain production continuity.
- Environmental sustainability
In response to the growing environmental issues, plastic cup manufacturers are increasingly adopting sustainable practices. Compared with other processes, hot forming technology has inherent advantages in material efficiency and recyclability. In addition, environmentally friendly materials, energy-saving equipment, and waste minimization measures can help reduce the impact on the environment and enhance corporate responsibility.
The production of plastic cups using a plastic cup molding machine requires a holistic approach, including mechanical selection, material optimization, process improvement, quality assurance, equipment maintenance, and environmental management. By adopting these core aspects, manufacturers can harness the complexity of the industry, meet constantly changing consumer demands, and contribute to a sustainable future.