The hot melt adhesive stick production line and hot melt adhesive stick assembly line should be operated by trained and experienced personnel. Generally, the main machine is not allowed to operate without heating or adding materials to avoid scratches on the screw and barrel. In the event of a power outage and shutdown, if there is material inside the barrel, it should not be restarted. The screw should be heated to the specified temperature before restarting to avoid twisting the screw and damaging the gearbox, which could cause accidents

Manufacturer of automatic hot melt adhesive production line
Hot melt adhesive can be divided into block shaped, granular, bar shaped, and powder shaped according to product shape.
Types of hot melt adhesive: EVA type (ethylene vinyl acetate copolymer), TPR (thermoplastic rubber), APAO type (polyolefin), PA type (polyamide), PU type (polyurethane), POLYester type (polyester), PE type (polyethylene) and others
What equipment is required for a complete production line of hot melt adhesive (block):
Reaction kettle (or kneading machine), mixing storage tank (optional), coarse filter, high viscosity pump, fine filter, roller conveyor, heating system, vacuum system, etc.
The heating methods used in the production of hot melt adhesive can be divided into: electric heating inside the jacket, electric heating oil heater, and thermal oil furnace (fuel oil, gas). The temperature of the heat transfer oil is generally controlled between 160-200 ℃, and the temperature of the material inside the kettle is controlled between 130-160 ℃.
Application scope of hot melt adhesive:
1) Packaging: cardboard boxes, food packaging, etc;
2) Sanitary products: diapers, sanitary napkins, etc;
3) Book and periodical binding: wireless binding of books and periodicals;
4) Wood furniture: plywood, wood flooring splicing, furniture fitting;
5) Automotive use: headlights, glass, filters, interior decorations, etc;
6) Textile products: adhesive, printing, adhesive backing;
7) Reflective materials: traffic signs, warning protective clothing, etc.
The process flow of the hot melt adhesive (block) production line is as follows:
1) Weigh the raw materials according to the proportion of the hot melt adhesive formula and add them to the reaction kettle (or kneading machine). Heat it up through a heating system to melt it, stir and mix evenly. Remove the bubbles inside the glue by vacuuming.
2) The melted adhesive material in the reaction kettle (or kneading machine) is pumped through the discharge pump and filtered into the packaging die (or into the mixing storage tank, and then to the packaging die), placed in the packaging box, and the packaged hot melt adhesive is cooled.

What equipment is required for a complete production line of hot melt adhesive (granular):
2 sets of reaction vessels (or kneading machine+mixing storage tank), coarse filter, high viscosity pump, fine filter, discharge die (or extruder), cooling water tank, traction granulator, vibrating screen, vibrating fluidized bed, cyclone separator heating system, vacuum system, etc.
The process flow is as follows:
1) Weigh the raw materials according to the proportion of the hot melt adhesive formula and add them to the reaction kettle (or kneading machine). Heat it up through a heating system to melt it, stir and mix evenly. Remove the bubbles inside the glue by vacuuming.
2) The melted rubber material in the reaction kettle is pumped through the discharge pump, filtered through the filtration system, and enters the mixing storage tank. After cooling to a certain temperature and maintaining a constant temperature, it enters the discharge die (or screw extruder) through the discharge pump.
3) The rubber strip extruded from the die (or extruder) enters the cooling water tank for cooling, and is pulled and cut by the traction granulator. The discharge speed and traction speed are controlled by a frequency converter to keep them synchronized. The particle size and length are controlled by the discharge hole of the die and the cutting speed of the cutter. The cut particles are cooled again and enter the vibrating screen for dehydration.
4) The dehydrated particles enter the vibrating fluidized bed and are dried by vibration and blowing with a blower. If further drying is required, they enter the cyclone separator for dehydration and packaging.
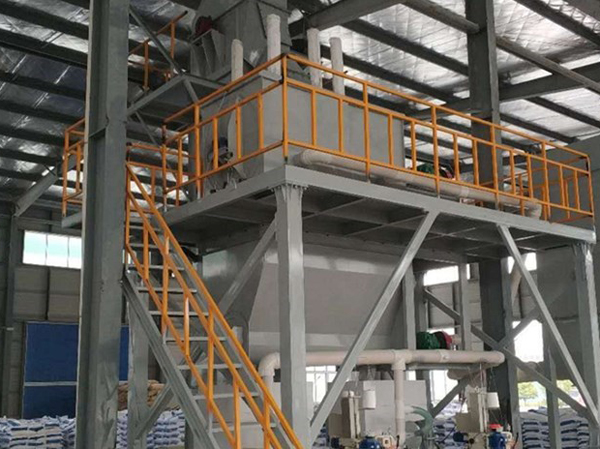
What equipment is required for a complete production line of hot melt adhesive (strip): 2 sets of reaction vessels (or kneading machines+mixing storage tanks), coarse filters, high viscosity pumps, fine filters, screw extruders, cooling water tanks, traction cutting machines, heating systems, vacuum systems, etc.
The process flow is as follows:
1) Weigh the raw materials according to the proportion of the hot melt adhesive formula and add them to the reaction kettle (or kneading machine). Heat it up through a heating system to melt it, stir and mix evenly. Remove the bubbles inside the glue by vacuuming.
2) The melted rubber material in the reaction kettle is pumped through the discharge pump, filtered through the filtration system, and enters the mixing storage tank. After cooling to a certain temperature and maintaining a constant temperature, it enters the screw extruder through the discharge pump.
3) The rubber strip extruded by the extruder enters the cooling water tank for cooling, and is pulled and cut by the traction granulator. The discharge speed and traction speed are controlled by a frequency converter to keep them synchronized. The size and length of the rubber strip are controlled by the extruder discharge hole and cutting blade speed.
4) The dehydrated particles enter the vibrating fluidized bed and are dried by vibration and blowing with a blower. If further drying is required, they enter the cyclone separator for dehydration and packaging.
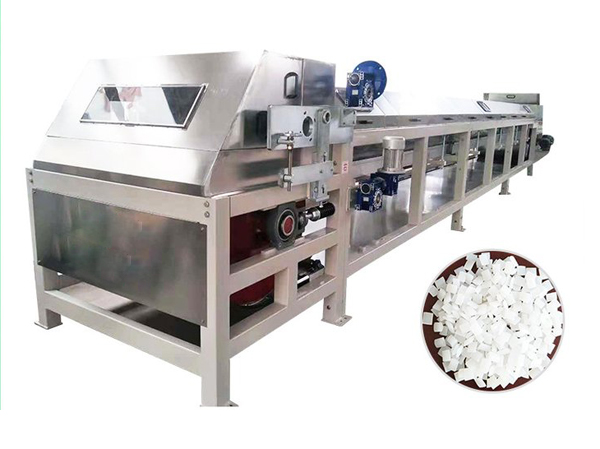
What equipment is required for a complete production line of hot melt adhesive (strip):
2 sets of reaction vessels (or kneading machine+mixing storage tank), coarse filter, high viscosity pump, fine filter, screw extruder, cooling water tank, traction cutting machine, heating system, vacuum system, etc.
The process flow is as follows:
1) Weigh the raw materials according to the proportion of the hot melt adhesive formula and add them to the reaction kettle (or kneading machine). Heat it up through a heating system to melt it, stir and mix evenly. Remove the bubbles inside the glue by vacuuming.
2) The melted rubber material in the reaction kettle is pumped through the discharge pump, filtered through the filtration system, and enters the mixing storage tank. After cooling to a certain temperature and maintaining a constant temperature, it enters the screw extruder through the discharge pump.
3) The rubber strip extruded by the extruder enters the cooling water tank for cooling, and is pulled and cut by the traction granulator. The discharge speed and traction speed are controlled by a frequency converter to keep them synchronized. The size and length of the rubber strip are controlled by the extruder discharge hole and cutting blade speed.