The fully automatic inorganic insulation paste mortar production line is equipped with inorganic equipment, and the overall layout adopts a tower type structure with a bucket elevator for feeding.
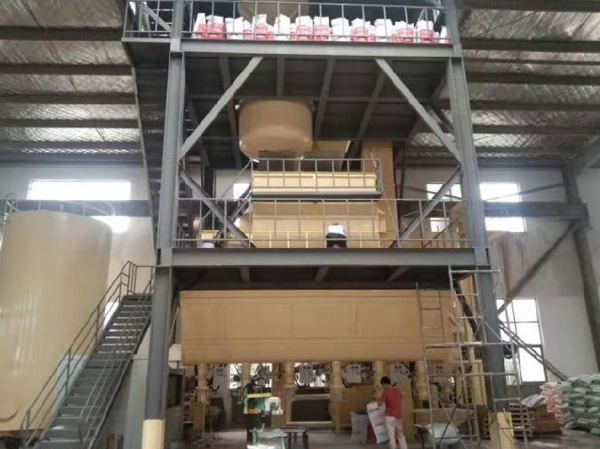
Manufacturer of automatic inorganic insulation paste mortar production line
Inorganic insulation paste mortar is a new type of insulation material. Inorganic paste insulation material is non flammable, safe and harmless, and does not release harmful substances, which meets environmental protection requirements. The inorganic insulation paste mortar production line equipment designed and produced by our company generally adopts a tower type structure. Various raw materials are weighed and proportioned, and then enter the high-speed disperser through a bucket elevator for primary mixing, and then enter a specially customized paste mortar mixing host for secondary mixing. The mixed paste mortar is quantitatively packaged through the filling port, and the packaged finished products are transported to the finished product area for stacking and waiting to leave the factory.
Inorganic insulation mortar equipment is used for producing vitrified microsphere insulation mortar or hollow microsphere insulation mortar. This product is also suitable for cement-based, gypsum based mortars and powders with lightweight and fragile particles. The complete set of inorganic insulation mortar equipment mainly consists of a mother material mixing system, a storage system, a copolymer mixing system, a vacuum negative pressure conveying system, a metering system, a packaging system, a dust removal system, etc.
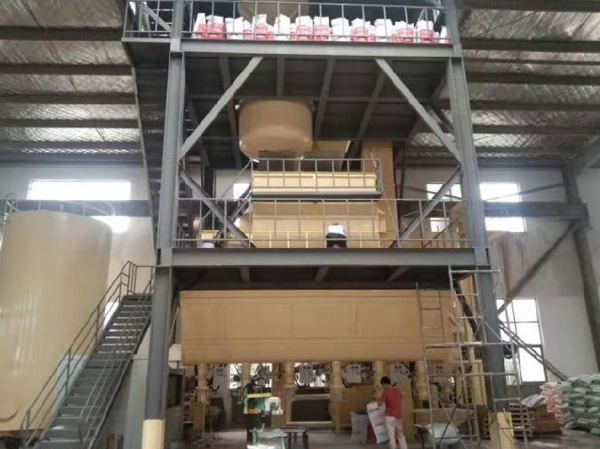
Inorganic insulation mortar is a new type of insulation and energy-saving mortar material used for painting the interior and exterior walls of buildings. It uses inorganic lightweight insulation particles as lightweight aggregates, and dry powder mortar composed of cementitious materials, crack resistant additives, and other fillers. It has excellent performance in energy conservation and waste utilization, thermal insulation, fire prevention and antifreeze, aging resistance, and low price, and has a wide market demand. The complete set of inorganic insulation mortar equipment is mainly used for producing vitrified microsphere insulation mortar or hollow microsphere insulation mortar, and is also suitable for cement-based, gypsum based mortar and powder with lightweight and fragile particles. The complete set of inorganic insulation mortar equipment mainly consists of a mother material mixing system, a storage system, a copolymer mixing system, a vacuum negative pressure conveying system, a metering system, a packaging system, a dust removal system, etc.
The inorganic insulation mortar masterbatch is mixed once using a gravity free mixer, and the mixed masterbatch enters the high-level tank through a bucket elevator. The vacuum negative pressure system sucks the raw materials and materials from the micro bead pool into the centrifugal mixer for shaftless mixing. Due to the pre mixed raw materials, the finished product has a short mixing time and high mixing uniformity. The mixed finished materials enter a specially designed finished material bin, which can reduce the pressure of the raw materials and evenly enter the vitrified microsphere packaging machine. The crushing rate of finished materials is low, the difference in material bulk density is small, and it is currently the most scientific and practical complete set of inorganic insulation mortar equipment with a unit area usage.