The fully automatic insulation mortar production line refers to the mortar equipment used for producing the insulation required for building walls. It can ensure the efficient and accurate production process of insulation mortar, and can meet the insulation needs of different buildings.
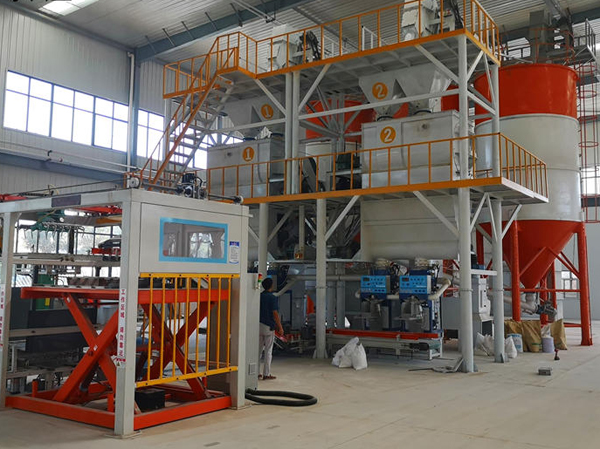
Manufacturer of automatic insulation mortar production line
The various sets of dry powder mortar equipment produced by our factory have the characteristics of small footprint, reasonable structure, simple operation, high production efficiency, no dust, and reasonable power configuration. Compared with the simple type, it is further advanced because the mixer automatically measures and packages the mixture through a valve pocket packaging machine or an open pocket packaging machine after mixing. It can be transported to the finished product stacking area using a belt conveyor. It has the characteristics of moderate investment, short construction period, and fast investment return. The equipment investment is generally between 20000 and 350000 yuan, and the output can reach 5-15 tons per hour. 3-5 operators, equipment height between 6-10 meters, occupying an area of 20-30 square meters.
The insulation mortar production line can produce interior wall putty and exterior wall putty by adjusting the proportion of raw materials; Interior Wall Series: Ordinary Putty, Mirror Putty, Nano Sterilization Putty, Moisture Control and Air Filtration Putty, Negative Ion Putty, Dry Powder Mortar,. Type: According to different production volumes, it can be divided into: simple dry powder mortar production line (annual output of 3000-10000 tons) basic insulation mortar production line (annual output of 10000-500000 tons) automatic insulation mortar production line (annual output of over 1 million tons)
The insulation mortar production line mainly consists of the following equipment:
- Raw material storage equipment is used in the putty powder production line to store bulk raw materials. Generally, tank design is used, and tank trucks are used for loading. During construction, only two small storage tanks for raw materials, such as rubber powder and additives, need to be added to store small amounts of raw materials.
- Ingredient device: It consists of a hopper measuring scale, a feeding dragon, a discharge device, a micro material addition device, and a computer control system. It can automatically measure different raw materials according to the formula, reducing labor intensity and environmental pollution, and ensuring the product quality of putty powder.
- Mixer: There are multiple options for mixers, such as double helix cone mixer, plow blade mixer, screw belt mixer, dual axis blade gravity free mixer, etc. The requirements for the putty powder mixer are: uniform mixing, no dead corners, high efficiency, wear-resistant equipment, and fast unloading speed. The above mentioned mixers are more commonly used in the putty powder production line, including the double axis slurry blade non gravity mixer and the plow blade mixer. Recommendation: Gravity free mixer – suitable for mixing dry powder, and can also add “flying knives” according to requirements. Plowing mixer – suitable for mixing and liquid mixing of materials with fibers.
- Packaging machine: There are two types: open pocket and valve pocket. Putty powder is commonly used in valve pocket packaging machines because valve pocket packaging does not require sewing and can be operated by one person. However, this packaging machine is not suitable for packaging lightweight materials, as the cost of the bag is slightly higher but the packaging speed is faster. The open pocket packaging scale can package various materials, but it needs to be sewn after bagging. Relatively speaking, the cost of bags is slightly lower (bags can be recycled), but the packaging speed is slightly slower. Compared with the valve pocket packaging machine, this packaging machine requires an additional operator.
- Dust collector: used to recover dust from the dry powder mortar production line, which is beneficial for environmental protection. Usually located on the top of cement silos, at the feeding port of elevators, etc. Recommended equipment: Bag pulse dust collector
- Conveyor and lifting structure: The material conveying methods used in production line silos include horizontal conveying and vertical conveying. Horizontal conveying can use a screw conveyor, while vertical conveying generally uses a bucket elevator.
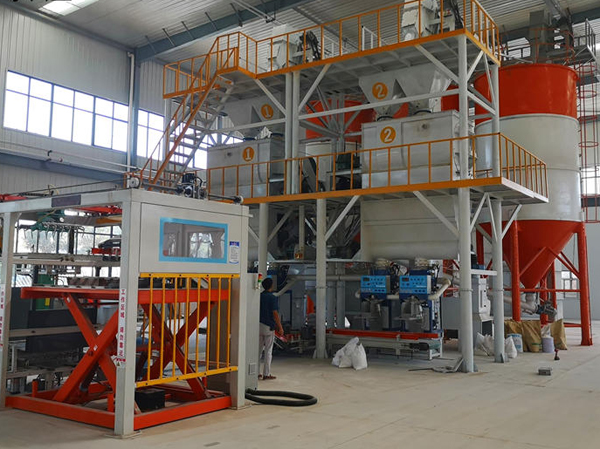
Advantages of insulation mortar production line
- The host adopts a cylindrical low-speed rolling operation, thereby avoiding damage to the vitrified microbeads during the production process;
- The host uses guide plates internally to evenly mix materials, resulting in short mixing time and high output;
- The mixing warehouse has a large capacity, with no dead corners or residues in the mixing process;
- Sealed well, with minimal dust, easy to operate, and convenient to maintain.
Structural characteristics of insulation mortar production line:
- Mixing system: The mixer adopts a drum type mixer, a large capacity mixing bin, short mixing time, high output, high uniformity, no residue, and no crushing.
- Lifting conveyor system: The lifting conveyor used in this project is a bucket elevator, which can effectively protect the weight standard of vitrified microbeads and improve the lifting speed.
- Dust removal system: The entire equipment is completely sealed without dust leakage, using multi-point dust collectors to collect dust from both the feeding and discharging ports, optimizing the working environment and ensuring the health of employees.