The complete set of equipment for lubricating oil production line consists of pressure saponification kettle, blending kettle, pipeline high shear homogenizer, heating system, cooling system, vacuum degassing system, conveying system, filtration and filling system, control system, etc. It is a specialized equipment for various types of biological lubricants, mineral lubricants, and synthetic lubricants.
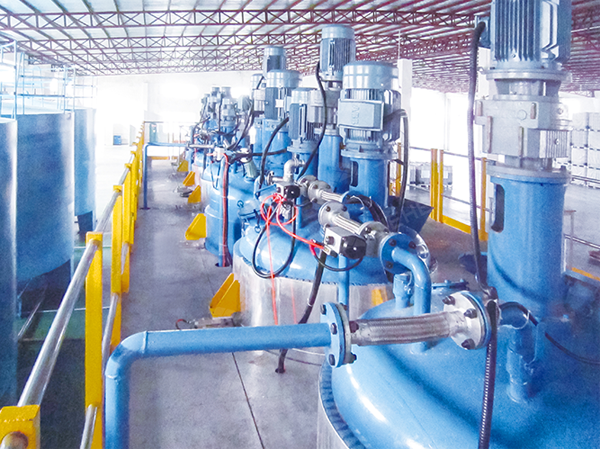
Manufacturer of automatic lubricating oil production line
We provide complete sets of equipment for lubricating oil and grease synthesis for different purposes. We can refine and improve the production process package according to the customer’s basic process flow, conduct detailed design of the production line, and provide complete sets of equipment including tank farms and storage tanks, as well as installation and commissioning services Our non-standard mixing design capability and system integration capability ensure that we can provide you with the suitable temperature range, mixing effect, sealing and other indicators for your process needs, providing strong assistance to your lubricant factory.
Brief description of the complete process of lubricating oil equipment
- The raw materials (one or several types) are stored in various outdoor storage tanks, and are injected into the mixing kettle after being measured by a diaphragm pump and flow meter
- The heat transfer oil is heated by the boiler and continuously circulates through the coil to heat the reaction kettle. The temperature inside the reaction kettle is monitored by a temperature sensor, and under the control of the automatic control system, the temperature inside the reaction kettle is controlled within the process requirements
- By using frequency conversion speed regulation, the stirring blades can fully stir and mix the materials at an appropriate speed
- The product is filtered through the bottom discharge port and discharged, weighed and filled
Note: If necessary, vacuum dehydration and degassing processes can be added.
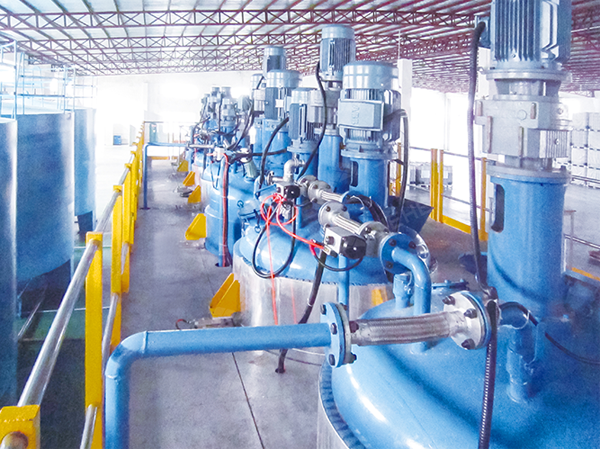
Lubricating grease is a stable solid or semi-solid product composed of a thickener dispersed in a liquid lubricant, in which additives and fillers aimed at improving certain characteristics of the grease can be added. Lubricating grease can adhere to vertical surfaces at room temperature without loss, and can work in open or poorly sealed friction areas, with a holding point that cannot be replaced by other lubricants. Generally speaking, lubricating grease with the same soap base has better compatibility. Organic clay base is incompatible with other bases. Therefore, lubricating grease, also known as butter, is used as a lubricating material in many parts of automobiles and construction machinery!
Lubricating grease is a stable solid or semi-solid product composed of a thickener dispersed in a liquid lubricant, in which additives and fillers aimed at improving certain characteristics of the grease can be added. Lubricating grease can adhere to vertical surfaces at room temperature without loss, and can work in open or poorly sealed friction areas, with a holding point that cannot be replaced by other lubricants. The lubricating grease production equipment mainly includes saponification reaction kettle, blending kettle, rapid cooling mixer, shear, homogenizer, degassing tank, vacuum pump, filter, thermal oil furnace, conveying pump, pipeline valve, etc.
Process flow of grease production equipment:
Taking lithium based grease as an example, lithium based grease is a type of grease that uses lithium soap as a thickener. Specifically, the production of lithium based grease can be roughly divided into the following steps: soap making – rapid cooling – blending – averaging – degassing – finished product packaging. First, the saponification reaction is carried out with lithium hydroxide and fatty acids (acids and bases). After the lithium soap is prepared, it is heated and dissolved into soap solution. Then, quench oil (base oil) is added to the soap solution for cooling. Finally, it is blended to become lithium based grease. However, at this time, the appearance of the lubricating grease is very rough and requires further post-treatment, namely homogenization and degassing, to finally obtain the finished lithium based lubricating grease.
- Saponification kettle (pressure grease kettle) : The pressure saponification kettle is a special saponification equipment for the manufacture of grease. It is designed and manufactured according to the national standard < steel pressure vessel >. This product has no central shaft, the use of gear transmission, no dead Angle, disassembly, replacement, maintenance is very convenient. The equipment is designed for the double-axis planetary stirring of the frame slurry, which is an advanced stirring device, which eliminates the past two-way agitator axis and the dead Angle attached to it, the frame is slow and the slurry is fast, and the ultra-wear-resistant edge scraper can effectively remove the attachments on the tank wall and greatly improve the heat transfer efficiency. The special heating jacket is equipped with a guiding ring to strengthen the rapid heat transfer effect, save energy, double point temperature measurement, two meters pressure measurement, double sight mirror, heat transfer oil or steam jacket heating is mainly used to complete the saponification reaction in the preparation of grease, for many processes in the petroleum, chemical, pharmaceutical and other industries.
Features: 1. Planetary stirring, automatic scraping, stirring evenly, thorough reaction. 2. Circulating oil heating, with high temperature, energy saving, environmental protection, safety and other characteristics. 3. Adopt advanced mechanical seal, high pressure, reliable sealing without leakage. 4. Packing seal, double feeding port, easy to operate.
Second, static clipper: at a certain temperature and a certain pressure through the clipper to cut the soap grain thicker products can make the soap fiber fully dispersed, effectively improve the appearance of the product.
Mixing kettle: mixing kettle stirring system is a two-axis planetary stirring, the frame is equipped with a flexible scraper, the jacket is equipped with a diversion ring to strengthen heat transfer, two points of temperature measurement, the difference between the two is: according to the production process is different, in the design of the bottom of the kettle mixing, stirring speed and the jacket medium is different, saponified kettle jacket through steam or heat transfer oil, two adjusted kettle jacket is through cooling water. It is mainly used to complete the harmonic reaction in the preparation of grease, and can also be used in many processes in the petroleum, chemical, pharmaceutical and other industries.
Fourth, the role of the quench mixer is that the hot soap liquid and quench oil are fully mixed once in contact to implement the disguised phase process, and both ends of the mixer can be used as an import and export. Liquid soap gear pump and oil cooled gear pump inlet valves are gate valves. The function of the quench mixer is to fully mix the hot soap liquid and quench oil once in contact to implement the disguised phase process, and both ends of the mixer can be used as an import and export. Liquid soap gear pump and oil cooled gear pump inlet valves are gate valves. Properly open the soap liquid valve to a certain extent, use the cold oil valve to adjust the quenching oil amount to the ideal value, the quenching mixer outlet temperature is recommended to be about 180 degrees, and the quenching oil amount is recommended to be about 1/3 of the total amount. After mixing, the temperature of the kettle is about 160 degrees. The sample can be viewed as transparent and delicate. If conditions permit, adjustable displacement gear pump can be used for cold oil pump and liquid soap pump.
Sleeve filter: the last filter device in the grease production process, composed of an inner cylinder and an outer cylinder. The inner cylinder is wound with a layer of 60-120 mesh metal mesh, so that the grease enters the homogenizer through this mesh, and the outlet of the homogenizer is connected with a vacuum degassing tank
Vacuum degassing tank: vacuum degassing tank is designed for negative pressure vacuum, and the working mode of spray feeding and vacuum pump pumping is adopted. The shape of the upper part is not small, the middle part is large, and the lower part of the cone is characterized by a pressure gauge port and an exhaust port.