The fully automatic thermoforming machine, also known as the thermoplastic forming machine, mainly uses the vacuum suction generated by the vacuum pump to heat and soften PVC, PET, PETG, APTT, PP, PE, PS and other thermoplastic plastic sheets into various shapes of vacuum covers through molds, or attach them to the surface of various shaped products. Vacuum forming is divided into thin sheet vacuum forming and thick sheet vacuum forming according to the thickness of the sheet.
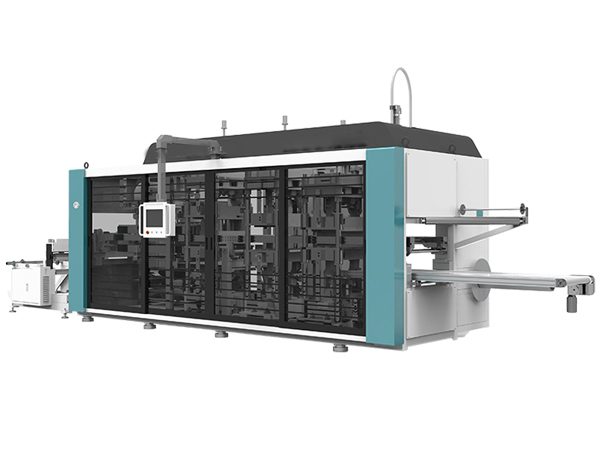
Manufacturer of automatic negative pressure thermoforming machine
Common products of thick sheet vacuum forming include: household appliance inner shells, luggage and bags, display rack accessories, decoration, car interiors, bumpers, fenders, beauty equipment, light box shells, toy car shells, industrial panels, advertising light boxes, vacuum formed logos, bathroom products, refrigerator inner shells, etc
Types of thermoforming machines
1、 Single male mold forming
Single male mold forming, also known as convex mold forming or bending forming, vertical forming. It is a molding method that uses machinery to shape plastic sheets that have been heated and softened into a certain shape.
2、 Single negative mold forming
Single negative mold forming, also known as concave mold forming.
3、 Die forming
The mold for molding is composed of a male mold, a female mold, fixtures, and other accessories.
4、 Composite molding
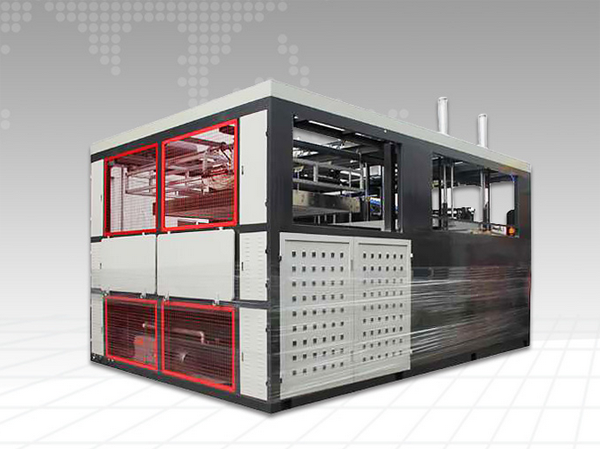
Thick Sheet Blister Thermoforming Machine
This machine is suitable for ABS, PS, PVC, PE, PP, PC acrylic and other sheet materials, and can produce and manufacture car mat interior parts, medical equipment shells, refrigerator liners, bathtubs, suitcases, etc.;
PLC control system is adopted, all process parameters, operation and settings are displayed on the touch screen, automatic manual state can be switched independently, and safety interlock protection function is equipped to prevent damage to the machine caused by operational errors;
adopts temperature control system, digital analog adjustment, can directly adjust parameters on the touch screen, and can store multiple sets of data, the temperature of each heating unit in the heating zone can be adjusted independently (one control, one precise control, more energy saving);
the use of fast and medium-wave infrared heating tube can be turned on and off, without preheating to heat up quickly. The electric furnace is only opened when entering the heating station. Upper and lower double electric furnace heating, combined with temperature control regulator, the heating temperature is constant and will not change due to voltage fluctuations;
. The anti-sagging function is adopted, and the heating state of the plastic plate is monitored by infrared rays to prevent the uneven thickness of the formed product caused by the sagging of the plate due to heat during the heating process. The mold table can be adjusted at will, thus shortening the mold change time and saving labor cost;
It adopts pre-blowing and core-pulling functions. For some products that are difficult to form, the thickness of the product after forming is more uniform and the quality is better. Blow back demoulding device, difficult demoulding mold can be easily demoulded, reduce the mold should be demoulded caused by damage;
The use of powerful fan and spray double cooling, can make the product faster and better, minimize inferior products, speed up the cooling rate, improve production efficiency.
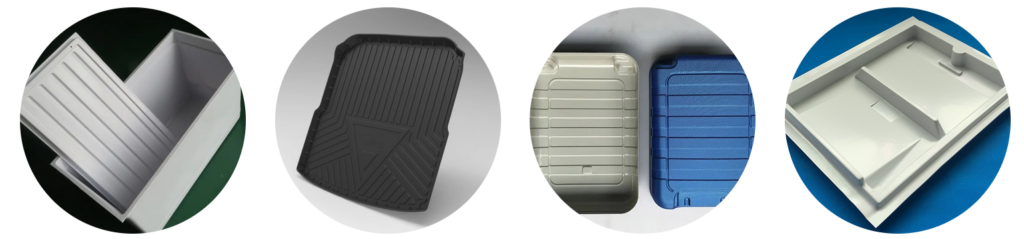
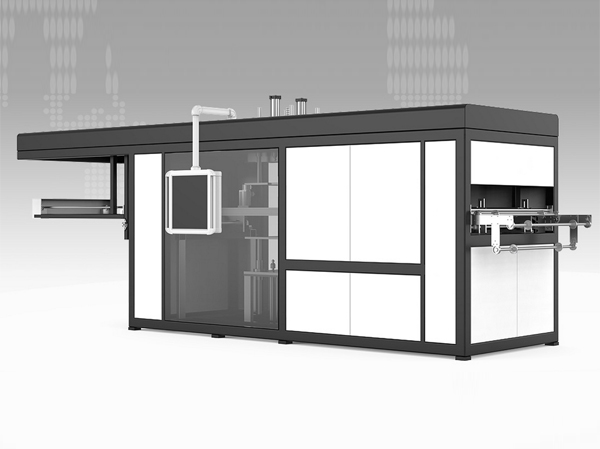
High Speed Servo Vacuum Blister Forming Machine
This machine is mainly designed for the molding and stretching stability of PP, PET and other environmentally friendly materials. The upper and lower dies are driven at a constant speed by servo motors to ensure high-precision product stretching and molding.;
adopts servo drive and full computer PLC control. It has storage memory, correction function (accuracy 1mm) and film exit function to avoid waste of film. The feeding adopts automatic design.;
In order to match the forming of different materials, the vacuum displacement adopts the complementary design of double body and valve, which ensures the rapid forming of stretch and difficult products.;
In order to ensure the molding stability of products with different rules, the mold is equipped with upper mold, top mold repetition or multiple frequency modes to choose from.;
electric furnace adopts a closed horizontal reciprocating design, and the temperature control adopts constant pressure independent control. The heating is stable and the supplement is uniform, which can effectively solve the undesirable waste phenomena such as whitening and deformation of PET materials and save more than 40% of electricity.;
Increase the cooling device and rapid cold water spray, and is equipped with auxiliary demoulding spray function, so that it can speed up the production speed, and the efficiency is more than 40% faster than the traditional machine.;
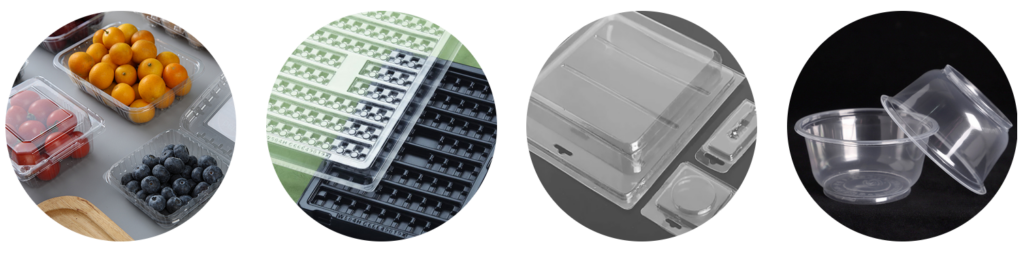
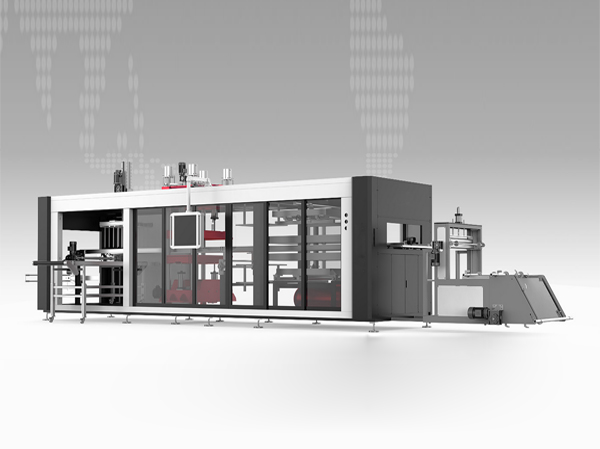
Three/four-station negative pressure thermoforming machine
the equipment integrates four stations: station, cutting station, punching station and stacking station, realizing full-automatic one-stop completion of sheet heating, forming, punching, cutting, stacking and counting;
the forming station, punching station and punching and shearing station are controlled by upper and lower servo motors. the driving eccentric wheel connecting rod structure drives the two die tables to move up and down respectively and is equipped with positive and negative pressure air sources, which can realize positive and negative pressure forming of products;
integrated, cutting, stacking, waste winding multi-station integration, sheet processing more smoothly, lower energy consumption;
the use of solid cast iron structure, with the crank arm roller bearings to ensure the perfect molding cutting;
The working table on the forming station is equipped with an independent servo-driven auxiliary stretching head to make the product more in place;
The forming station increases the tension rod structure, so that the forming station has the function of cutting in the mold, and at the same time ensures the longer service life of the cutting knife;
a variety of full-automatic stacking methods, such as upward stacking, AB stacking, complete cutting of products by manipulator, etc., can meet the diversified needs of customers for blanking and retaking.
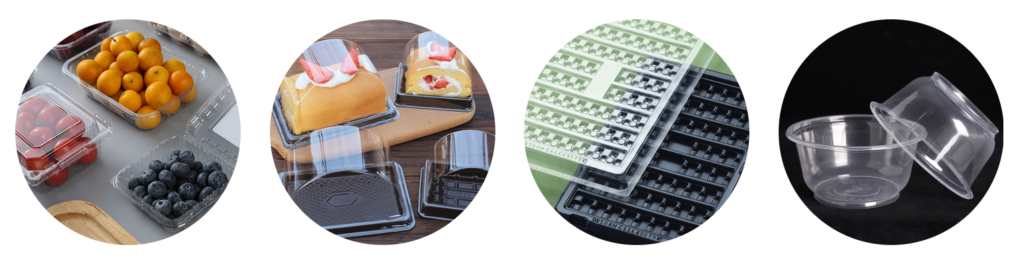