The paint spraying production line is an efficient and highly integrated industrial production system that can spray paint at high speed according to specific trajectories, flow rates, speeds, and shapes, so that the product surface is coated with anti-corrosion, durable, and aesthetically pleasing properties. The spraying line production equipment is divided into two types: local spraying production line and overall spraying production line, which are selected according to the spraying needs of different products.
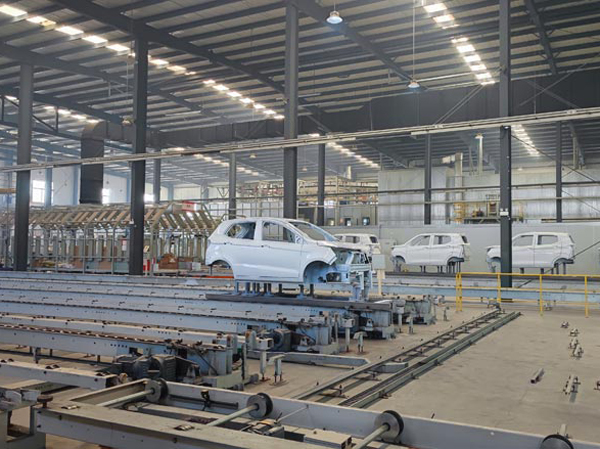
Manufacturer of automatic paint spraying production line
The equipment for paint spraying production line includes multiple components, such as spraying room, spraying device, air supply equipment, lighting equipment, ventilation equipment, spray gun, conveying device, heating equipment, dust removal equipment, and exhaust gas purification equipment.
Working principle of automatic spraying machine
Automatic spraying line is a modern spraying equipment that integrates pre-treatment, drying, spraying, curing, automated conveying system, computer control and other technologies.
By accurately controlling the spraying trajectory, spraying speed, and spraying amount of the spraying gun through a computer control system, uniform spraying of the workpiece surface can be achieved. The paint recycling system equipped with automatic spraying equipment can recycle and reuse unused paint, which can effectively reduce costs and increase efficiency as a whole.
Composition and Structure of Spray Production Line:
Manual loading and unloading, automatic conveyor line, manual dust removal/electrostatic automatic dust removal, preheating and dehumidification, automatic spraying equipment (reciprocating machines, robots, etc.), purification workshop, paint mist exhaust system, constant temperature and humidity air supply system, high-efficiency pressure equalization box, product surface leveling, drying, cooling system, central control system, wastewater and exhaust gas treatment system, etc
Details of Spray Production Line:
Coating applications: spray painting, powder coating, oil spraying, adhesive coating, etc
Spraying method: Select a reasonable automatic spraying equipment (reciprocating machine, robot, etc.) based on the spraying range of the product and the number of spray guns;
Transportation methods: suspension line, ground chain line, spindle line
Flat conveying (optional mesh, drum, belt, chain), etc;
Spray environment: The spray booth adopts a water curtain or dry, Class 10000, Class 100000 dust-free spray room, and is sent into the spray room through an efficient air supply outlet; Constant temperature and humidity, etc;
Baking methods: tunnel oven, precision oven, far-infrared heating IR tube, UV curing;
Waste gas treatment: spraying and activated carbon filtration before discharge;
Output: depends on the tooling method of the workpiece, the baking time of the coating, and factors such as line speed;
Suitable for surface painting treatment of products such as plastics, hardware, wooden products, glass, ceramics, magnets, etc;
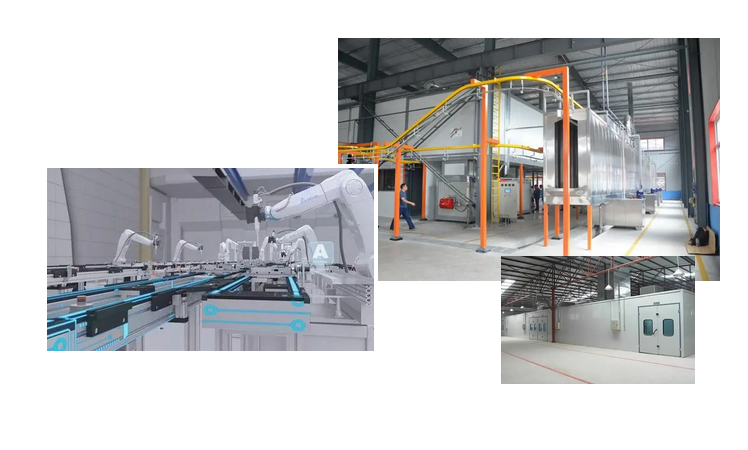
The working principle of the spraying production line can be divided into:
One is powder coating, also known as powder coating, which uses plastic powder as the raw material.
The second is painting, which involves applying a paint film on the surface of the workpiece.
Characteristics of powder spraying process
advantage:
(1) A single coating can obtain a thicker coating, for example, coating with a thickness of 100-300 μ m. Using ordinary solvent coatings requires about 4-6 coats, while using powder coatings can achieve this thickness in one coat. The corrosion resistance of the coating is very good.
(2) Powder coating does not contain solvents, has no three waste pollution, improves labor hygiene conditions, and has minimal harm to the environment and human health.
(3) After using electrostatic spraying, the coating quality is better and the adhesion is stronger.
(4) Powder electrostatic spraying and other processes have high efficiency, high automation level of automatic assembly line coating, high powder utilization rate, and can be recycled
(5) Short curing time, no liquid sagging, and high appearance quality of the finished product.
Main disadvantages: The sprayed surface is not easy to repair and has a high cost.
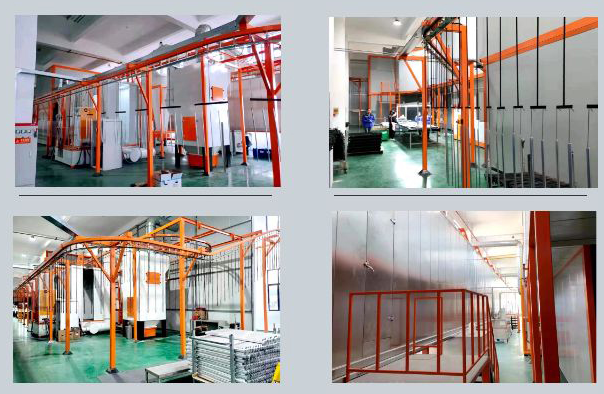
Automatic spraying equipment has the following advantages:
1.High accuracy: The automatic spraying equipment uses a PLC control system to accurately control the flow rate, spraying distance, and spraying time of the coating, achieving high accuracy requirements.
2.High precision: The automatic spraying equipment is equipped with an automatic cleaning device, which can eliminate the interference of dust, stains or other impurities on the spraying process, thereby achieving higher coating accuracy and making the coating process smoother.
3.High efficiency: Automatic spraying equipment uses high pressure during the spraying process, which can effectively increase spraying efficiency and greatly reduce spraying time.
4.Save materials: Automatic spraying equipment can automatically detect the flow rate, spraying distance, and spraying time of paint, which can effectively reduce excessive paint consumption and save costs.
5.Environmental Protection: Automatic spraying equipment can be applied to most non-toxic and harmless coatings on the market, effectively reducing pollution to the environment and lowering environmental load.
The application prospects of automatic spraying production line
With the transformation and upgrading of the manufacturing industry and the continuous improvement of environmental protection requirements, automatic spraying lines, as an efficient, coating saving, and labor-saving spraying equipment, have a very broad application prospect.
1.Automotive parts industry: Automotive parts manufacturing is one of the important application areas of automatic spraying lines. At present, with the continuous increase in market demand for automobile production and consumers’ increasing demand for automobile appearance quality, automatic spraying lines will be more widely used in the automotive industry.
2.Home appliance and cookware industry: The requirements for coatings on home appliances are increasing day by day, and automatic spraying lines can meet the requirements for coating uniformity, aesthetics, and durability of home appliances and cookware products, as well as large-scale production capacity.
3.Furniture industry: The furniture industry has always had high requirements for coating technology. Automatic spraying lines can achieve uniform spraying and personalized customization of furniture surfaces, and the stacking production mode can greatly reduce factory floor space and improve production efficiency.
4.Hardware machinery equipment: Due to the high requirements for surface anti-corrosion, there is a large demand for automated painting lines for hardware machinery equipment. Automatic spraying lines can achieve fast and uniform spraying of hardware surfaces, improving production efficiency and quality.
Automatic spraying lines are playing an increasingly important role in the manufacturing industry due to their high efficiency, low coating costs, and labor-saving features. With the continuous advancement of technology and the expansion of application fields, automatic spraying lines will have broader market prospects and application space.
Automatic spraying production line is an efficient and precise coating equipment widely used in various industrial fields, providing high-quality surface coatings for products. It achieves fast and uniform spraying of workpieces through automated control systems and precise spraying technology, greatly improving production efficiency and product quality.
The core components of an automatic spraying production line include spraying equipment, conveying system, control system, etc. The spraying equipment is responsible for completing the coating spraying work, and its performance directly affects the quality and effect of the coating. The conveying system transports the workpiece to be sprayed to the working area of the spraying equipment, ensuring that the workpiece can be sprayed according to the predetermined path and speed. The control system is the “brain” of the entire production line, responsible for coordinating the work of various components and ensuring the stable operation of the production line.
The fully automatic spraying machine is a product of the development of the times and technology. With the continuous growth of automation technology, computer technology, and human capital, the previous application of glue coating was done manually or semi automatically. Therefore, fully automatic spraying machines have emerged to meet the needs of the times.
Air spray guns can be divided into three types according to the feeding method: pressure type, siphon type, and gravity type. The pressure type spray gun delivers the paint to the spray gun through the pressure of the pressure tank or double barrier pump. The spray gun itself does not come with a can, which reduces the weight of the spray gun and lowers the labor intensity of the operation. It is suitable for continuous and discontinuous operation, preventing material addition from causing work stoppage, improving work efficiency, and achieving excellent spraying quality. Capable of operating the spray gun from any position and angle. The lower part of the siphon spray gun is equipped with a coating tank, and compressed air creates a low-pressure vacuum in the front half of the spray gun. Atmospheric pressure draws the coating from the coating tank to the spray gun. The coating tank is divided into two types: 600ml and 1000ml, which can be selected according to the size of the spraying amount. The spray gun can work with compressed air without the need for other equipment. But it can only be operated at a normal level, and the inclination of the spray gun is limited. Siphon type is suitable for various coatings.
The upper part of the gravity spray gun is equipped with a paint tank, which delivers the paint to the spray gun by gravity. According to the position of the paint tank relative to the axis of the spray gun, it can be divided into side type and type. During operation, the tilt of the spray gun is restricted by the formula, while the side type allows the operator to stop spraying at different positions while the paint tank remains vertical. The drawback of the side type is that the size of the paint tank is relatively small, usually 400ml, and the consumption efficiency is low. But the major advantage of gravity based coating is minimal waste of paint. Cleaning is very convenient and consumes less solvent.
During the operation of the automatic spraying production line, the workpiece first enters the spraying area through the conveying system. The spraying equipment accurately sprays the workpiece based on preset spraying parameters, such as spraying speed, spraying distance, spraying angle, etc. During the spraying process, the spraying equipment will adaptively adjust according to the shape and size of the workpiece to ensure that the coating can evenly cover the surface of the workpiece. At the same time, the spraying equipment will adjust the spraying parameters in real time according to the properties of the coating and environmental conditions to achieve the best spraying effect.