The fully automatic pre mixed mortar production line can accurately mix the required dry mortar according to the formula requirements through computer measurement, and then mix it with the mixing host to produce the required dry mortar in real time. Most special mortars can also be manufactured according to the formula. The entire process adopts an automated operation mode.
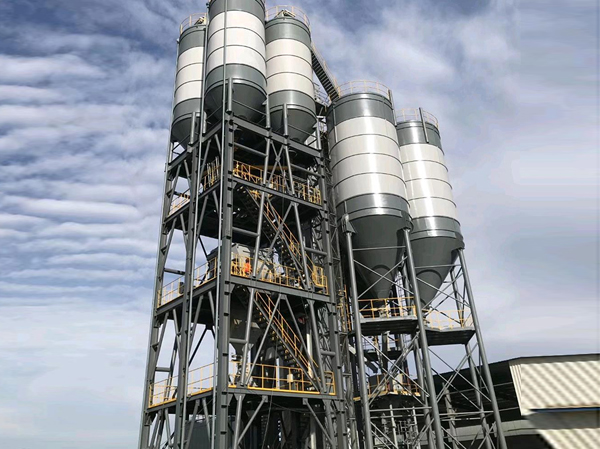
Manufacturer of automatic pre mixed mortar production line
The process characteristics of the dry mix mortar production line, combined with domestic and foreign technology and experience accumulation, have launched a new fully automatic energy-saving dry mix mortar complete set of equipment. This equipment can be used in conjunction with dry sand making systems or wet sand drying systems to produce high-quality and high standard dry powder mortar and special mortar. The main building adopts a tower structure, and the powder silo is installed on the top of the main building. The additive system adopts an independent platform for metering and pumping. The aggregate passes through the measuring layer, mixer layer, finished product warehouse, control room, bulk loader, and packaging machine from top to bottom.
The use of pre mixed mortar production lines can bring numerous advantages. Firstly, the pre mixed mortar production line can ensure the uniformity and consistency of concrete and mortar, thereby improving the quality and strength of the project. Secondly, the pre mixed mortar production line can achieve automated production, greatly reducing manual workload and improving production efficiency. In addition, the pre mixed mortar production line can also save raw materials, reduce waste generation, lower engineering costs and environmental pollution.
When choosing a pre mixed mortar production line, there are some important points to consider. Firstly, it is necessary to determine the scale and production capacity of the production line based on actual demand. Secondly, it is necessary to select reliable equipment suppliers and conduct strict inspections on the quality of their products. In addition, it is necessary to pay attention to the maintenance and after-sales service of the equipment to ensure its long-term stable operation.
The pre mixed mortar production line is a comprehensive equipment mainly used for the production of concrete and mortar. It consists of multiple modules, including raw material processing, mixing, complete mixing, and transportation. During the production process, pre configured raw materials undergo a series of processing and mixing to ultimately produce high-quality pre mixed mortar. Pre mixed mortar production lines are usually composed of mixers, measuring systems, conveying equipment, and control systems. The functions of each module are interconnected to form an efficient and automated production line.
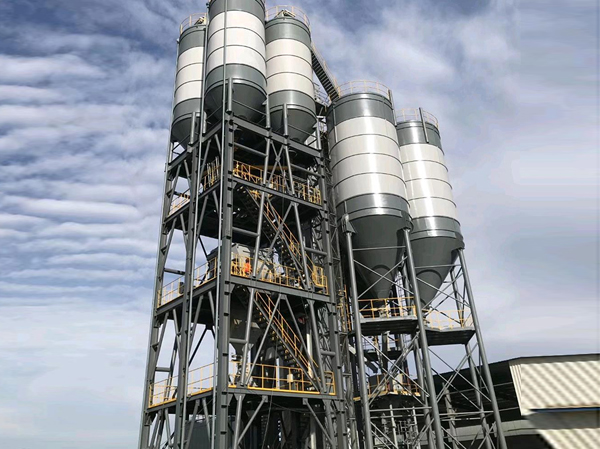
Production process description of dry mixed mortar
- Aggregate drying:
A. Sand three return dryer, with an hourly output of 60 tons. The dryer adopts a three sleeve structure, which significantly shortens the length of the equipment, reduces the footprint, and improves the heat utilization rate.
B. The variable frequency speed control belt conveyor is used for feeding, and the feeding speed is adjusted according to the moisture level of the aggregate to ensure that the moisture content of the discharged material matches the drying output.
C. Large dust collection, high ventilation, improve dust removal efficiency, and protect the environment.
D. Select heat sources according to local conditions. There are two options, one is the accessory boiling furnace, which is used to burn biofuels or coal; The second is to be equipped with a combustion chamber for burning natural gas or oil.
E. The dried aggregate is sieved and roughened before entering the elevator. The screening machine can be equipped with a vibrating screen or a cylindrical screen.
- Material reserve:
A. Four aggregate storage bins are used to store different types or gradations of aggregates. Such as machine-made sand, river sand, industrial tailings, etc. In practical use, the selection of sand sources and optimization of mix design are carried out. Each sub warehouse is equipped with accessories such as high and low level gauges and exhaust hoods.
The aggregate is dried by a drying system to remove moisture, and excess particles are screened out as required. It is then stored in the corresponding silo through a bucket elevator and distributor.
B. There are four powder storage warehouses, one for cement, one for mineral powder, one for desulfurization gypsum, and one for mortar special additives (thickening powder): desulfurization gypsum is a waste from power plants, which can be used for mortar production after treatment and can replace cement. It not only treats waste, but also reduces material costs.
The powder is transported by the pneumatic conveying system of the transport vehicle and sent to the corresponding silo for storage.
Each sub warehouse is equipped with high and low level gauges, dust collectors, explosion-proof safety valves, arch breaking devices, manual butterfly valves, and conveying pipelines and other accessories.
C. Additive: Three additive storage bins are set up, and the additive is transported to the top of the bin by a box type elevator and manually added. Used in the production of different special raw materials or mortar, expanding the range of raw material selection and producing multiple varieties of finished products.
D. Trace additives are added using a primary additive addition device, which is placed on the ground and includes storage, metering, and delivery devices for mortar additives.
- Raw material measurement and addition:
The measurement layer of this system is equipped with one sand measurement scale, one powder scale, and one additive scale. The aggregate enters the weighing hopper from the silo through the pneumatic valve port; Powder materials are fed separately by screw conveyors to the weighing hopper for measurement. Micro automatic measurement and addition, reducing measurement errors to around 5 grams.
- Mixing system:
This system adopts a high-efficiency mortar mixer, model LD-3000, with a maximum batch mixing mortar weight of 3000 kg, and a large door mechanism for unloading. Set up a gas phase equilibrium system.
- Finished product processing:
After being mixed and blended evenly, the mortar is discharged from the mixer into the finished product hopper and divided into two paths through a pneumatic three-way valve:
All the way through the bulk loader, it enters the bulk truck and is transported to the construction site. The other route passes through a horizontal screw conveyor and is transported to the packaging transition warehouse for packaging.
- Finished product packaging:
The materials are transported from the finished product warehouse to the packaging storage warehouse through a screw machine. There are two valve packaging machines under the packaging storage warehouse, and the packaged finished product bags are sent to the finished product workshop through a belt conveyor.
3、 Dust removal system
- Top layer of silo: Each powder silo is equipped with a dust collector.
- Measurement system: The measured materials are transported by closed chutes and screw conveyors, and dust collection devices are installed for the discharge and exhaust of each weighing hopper.
- Finished product layer: The bulk machine and packaging machine share one dust collector.
- The exhaust gas from the dryer is separated and dedusted through a two-stage cyclone bag, and the exhaust gas discharged when using coal as fuel is desulfurized through a desulfurization tower.
4、 Computer control system:
Taiwan, China Advantech Industrial Control Computer
Adopting imported specialized electronic scale batching control instrument (PT650D)
The computer control system realizes automatic control and complete manual support for the entire process of metering, unloading, conveying, mixing, and discharging.
Capable of printing statistical production daily reports, monthly reports, querying raw production data, and comparing material measurements. Design the invoice format for the delivery note according to user requirements
The main components used in the high-voltage cabinet and control panel are Schneider products.
It can store 1000 formulas and plan numbers, which can be called and modified at any time.
Dynamic simulation process. Equipped with computer self diagnosis and alarm functions.
It has the function of automatic correction of differences to ensure accuracy.