The special mortar produced by the fully automatic special mortar production line is suitable for special requirements such as insulation, sound absorption, waterproofing, corrosion resistance, and bonding in dry mixed mortar.
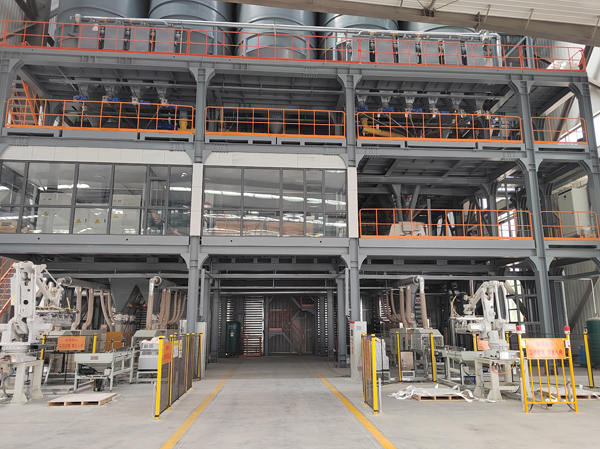
Manufacturer of automatic special mortar production line
There are many types of special mortar:
Cement based special mortar types: bonding mortar, tile adhesive, waterproof mortar, crack resistant mortar, self leveling mortar, thin layer plastering mortar, etc
Putty powder: exterior wall putty (with sand mold, no sand mold), interior wall putty (water-resistant, non water-resistant), surface putty, bottom putty, etc.
Gypsum mortar: lightweight plastering mortar, heavy mortar, gypsum self leveling, etc
In addition, there are insulation mortar series, grouting materials, corrosion-resistant mortar, radiation resistant mortar, etc.
Due to the variety of special mortar types, a single production line is generally used to produce the same type of mortar, and it is advisable to avoid using multiple machines as much as possible.
The application fields of special mortar production lines are also very extensive, mainly including the following aspects:
Construction industry: Special mortar is widely used in the construction industry, including external wall insulation, sound insulation, waterproofing, fire prevention, etc.
Mining industry: Special mortar can be used in mining restoration, landfill closure and other fields.
Chemical industry: Special mortar can be used for maintenance and corrosion prevention of facilities such as storage tanks, pipelines, ponds, etc.
In short, the special mortar production line has broad application prospects and market potential, and will be increasingly valued and widely used in future development.
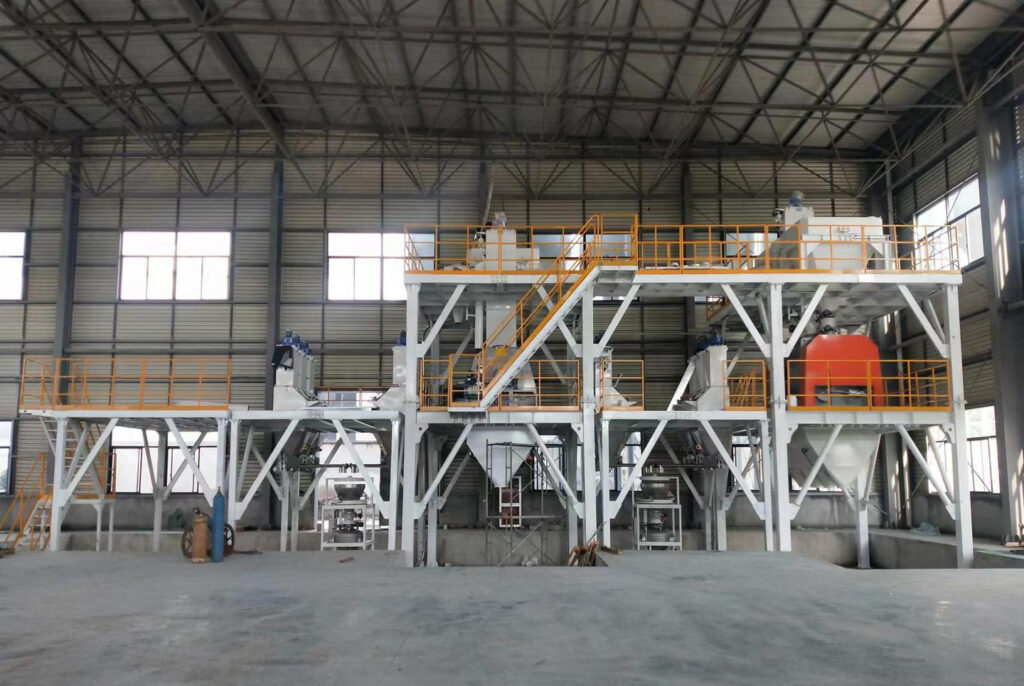
Main equipment of special mortar production line
Drying system:
Used for drying wet sand particles produced or collected, the system includes equipment such as a disc feeder, drying host, conveyor, screening machine, dust collector, elevator, etc.
Raw material tank:
Used for storing cement, fly ash, etc., using pump truck pneumatic feeding. The top of the warehouse is equipped with a dust collector, which can effectively protect the working environment. The conical part of the warehouse is equipped with a pneumatic arch breaking device, which can effectively prevent cement and fly ash from arching and ensure smooth metering and spiral batching.
Hybrid system:
The equipment host adopts an energy-saving dual axis blade type gravity free mixer, with a mixing uniformity of up to 99%. The machine has automatic feeding, pneumatic discharge, no accumulation or dead corners on the barrel wall during the production process, high uniformity, and can shorten the mixing time. It is currently an ideal mixing equipment.
Packaging system:
The produced finished products can be directly fed into the finished product storage bin through the lifting system, or packaged and stored in separate bags. Valve bag packaging machines are commonly used, which use computer measuring devices, have stable performance, simple operation, and are equipped with dust removal ports to reduce the harm of dust to human health and achieve environmentally friendly production.
Dust removal system:
Used for recycling dust generated in the production of dry mixed mortar, which is beneficial for the environmental protection of the production environment. Pulse bag filter is generally used, which operates reliably, has high dust removal efficiency, and is easy to maintain.
Conveyor and lifting system:
Used for material conveying in the production process of dry mixed mortar, it can be divided into horizontal conveying and vertical conveying. Horizontal conveying can use a screw conveyor, while vertical conveying generally uses a bucket elevator. The lifting process is fully enclosed to ensure a clean and environmentally friendly working environment.
Control system:
Adopting a convenient full computer PLC control system, the operation of each device is simulated and displayed, and the operating situation is clear at a glance, making the operation more effortless.
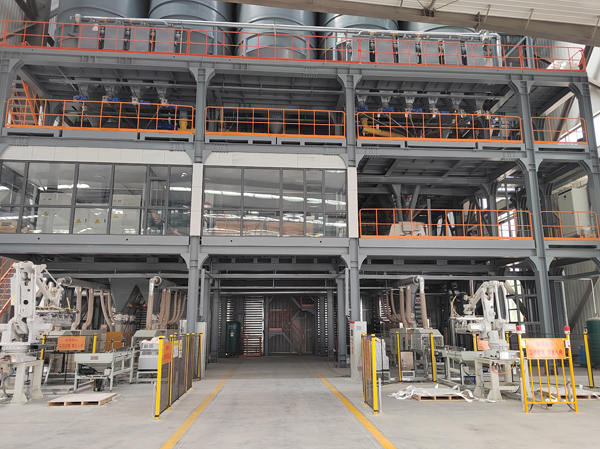
The special mortar production line is designed to produce various special mortars. Special mortar is a high-performance building material used in various special construction and decoration projects. Compared with traditional cement mortar, special mortar has higher strength, better durability, higher bonding strength, and better waterproof performance.
A special mortar production line usually consists of the following parts: raw material processing system, mixing system, conveying system, packaging system, and control system. The raw material processing system is used to process various raw materials, including cement, gypsum, quartz sand, cellulose, etc. The mixing system mixes raw materials to form special mortar. The conveying system transports special mortar to the packaging system for packaging. The control system is used to control the operation of the entire production line to ensure the quality and production efficiency of the special mortar produced.
The special mortar production line can produce various special mortars, such as waterproof mortar, high-temperature resistant mortar, acid alkali resistant mortar, self leveling mortar, etc. These special mortars are widely used in various construction projects, including underground engineering, water conservancy engineering, road engineering, bridge engineering, decoration engineering, etc.
The introduction of special mortar production lines can improve the production efficiency and quality of special mortar, meet the market demand for special mortar, and promote the development of the construction industry.