Dry mixed mortar mixing plant station, also known as mortar dry powder material, refers to a granular or powdery mixture of fine aggregate inorganic binder, water retaining thickening material, mineral admixture, and additives produced by manufacturers and processed by drying and screening in a certain proportion.
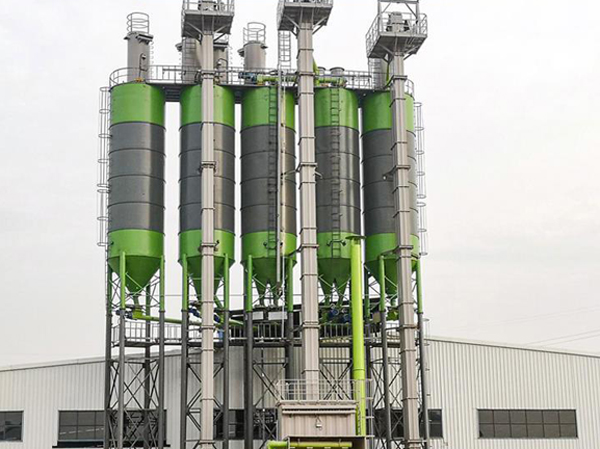
Manufacturer of dry powder mortar station
Simply put, it mainly consists of yellow sand, cement, thickened powder, fly ash, and additives. In addition, additives such as early strength agent and quick drying agent are added according to the variety requirements. It can be transported to the construction site in packaging or bulk, mixed with water according to the specified ratio, and can be used directly.
The dry mixed mortar station is a production line used for producing dry mixed commercial mortar, and its main components generally include the following parts:
- Wet sand pretreatment, drying and cooling, and storage;
- Storage of binders, fillers, and additives;
- Measurement of ingredients for main and auxiliary materials;
- Mixing and stirring;
- Packaging or bulk;
- Fully automatic process computer control system.
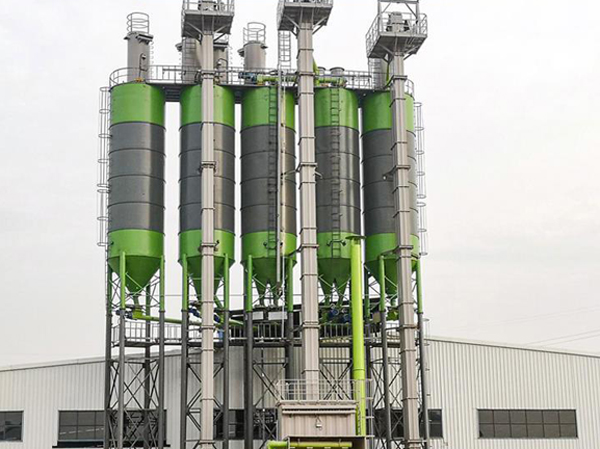
There are different plans for dry mixed mortar stations according to requirements and different markets. Commonly used layouts include station layout, stair step layout, tower layout, etc. The general process is to lift all pre processed raw materials to the top of the raw material silo, and rely on the weight of the raw materials to naturally flow out of the silo. After weighing, batching, mixing, packaging and other processes, it becomes the final product. All production is completed under the operation of modern microcomputer control systems. The operator only needs to specify the type and quantity of the product, and all other operations are automatically completed by the control system without manual intervention. All use enclosed production system equipment, clean the site, no dust pollution, ensuring the health of workers. The equipment has a modular structure, with a production capacity that can keep up with the development of the market. It has high ingredient accuracy, flexible use, and is easy to expand.
The drying system is a core component of the entire mortar station and a key point in determining overall production efficiency. Single drum dryers have gradually been phased out because they not only occupy a large area, but also consume high coal, and their only advantage is easy maintenance. With the maturity of the three tube dryer technology, the mainstream has started to use three tube dryers. The main manufacturers of three tube dryers include Xuzhou Tiandi Heavy Industry, Shanghai Shanshui, etc. The overall production efficiency of the three tube dryer is divided into series such as 20, 30, 40, 50, 60, etc. It refers to the hourly dry sand production. Generally, a 30 ton mortar can achieve a production capacity of 25-28 tons, so the amount of mortar that can be mixed is 35-40 tons.
The heat source for drying equipment can be selected from hot air stoves, boiling furnaces, etc. The cost of a hot blast stove is lower, but it requires good coal combustion and will not produce slag; Boiling furnaces are relatively expensive and can burn low-grade coal. The selection of drying equipment is mainly based on the local actual situation. If it is in a coal producing area and the environmental requirements are not strict, a boiling furnace can be used.
The screening system can use single-stage linear vibrating screen or graded screen, and some manufacturers also add a vibration crushing device to crush the screened coarse sand and recycle it. The key points for selecting a screening system are: according to the actual sand selection, if using general river sand without a crushing device, then a regular linear vibrating screen is sufficient. If stone powder needs to be used, it is best to use a drum screen.
The mixing system generally adopts two types: single axis pear knife type or double axis gravity free type. Both types of mixers can be used for mortar stations, but there are also important considerations when it comes to equipment selection. The single axis pear knife type mixing machine can mix more thoroughly, especially for some very trace additives, so it can be used to produce special mortar. The disadvantage is high cost and low mixing efficiency; The dual axis gravity free mixing host has the characteristics of high mixing accuracy, fast speed, low energy consumption, and sealable operation, and is suitable for producing ordinary mortar.
Other components include metering systems, bulk and packaging systems, dust removal systems, control systems, etc.
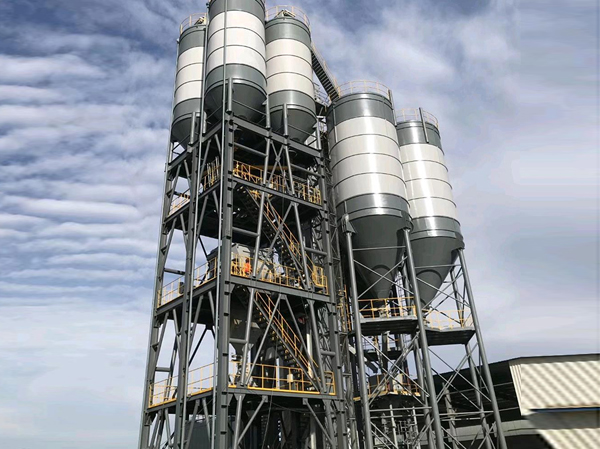
Building block production equipment
It is designed based on the factory building and investment scale of the manufacturer. Low cost and reasonable process. Automatic metering and computer operating system also need to be configured. We can produce exterior wall insulation mortar, self leveling mortar, repair mortar, waterproof mortar, colored decorative mortar, interior and exterior wall putty, tile adhesive, joint filler, and more. Suitable for medium-sized enterprises.
Tower style production equipment
The various systems of this type of production line are arranged from top to bottom according to their functions, including raw material storage system, metering and batching system, plow type mixer, bulk and packaging system.
① The raw materials are first transported to their respective storage bins through pneumatic conveying or bucket elevators.
② When measurement is required, the butterfly valve below the storage bin automatically opens, and the raw materials flow into the measuring scale (due to height restrictions and the inability of cement and other powder materials to effectively flow through the chute, a screw conveyor is used for transportation). The measuring scale closes the pneumatic butterfly valve under the bin when the raw materials are ready according to the preset program, and the measurement is completed.
③ After the previous batch of the mixer is mixed and the finished mortar is placed in the finished product buffer bin, the pneumatic valve under the measuring scale is opened, and the raw materials fall into the mixer to start mixing.
④ The mortar in the finished product buffer bin can be sent to the finished product loading machine, bagging and packaging machine, and finished product storage bin below through the distributor below.
Flat production equipment
A flat layout is relative to a tower layout, with a project area of approximately 8000-10000 square meters (12-15 acres), mainly consisting of a sand drying plant, drying plant, mixer, warehouse, office building, housing, etc. If the site is limited, 7.5 acres is sufficient.
A flat layout occupies a relatively large area compared to a tower layout, as various equipment is placed horizontally and materials are transported through various conveying equipment to enter the material bin, mixing, and bulk processes in sequence. The characteristics are relatively small investment, low height, and easy installation and maintenance. The area occupied is relatively large, and the materials are repeatedly lifted and transported, resulting in high energy consumption and difficulty in cleaning.