Lithium battery separator film production line: With the rapid development of electric vehicles and renewable energy, lithium batteries have been widely used and researched as a high energy density, environmentally friendly, and efficient energy storage device. As an important component of lithium batteries, the lithium battery separator plays a role in isolating the positive and negative electrodes, ensuring the safety and performance stability of the battery
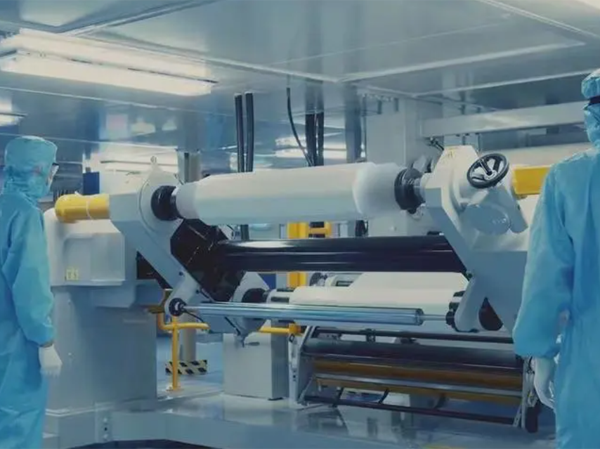
Lithium Battery Separator Film Production Line
The lithium battery separator production line is an equipment used to produce lithium-ion battery separators. The separator is the separator between the positive and negative electrodes of the battery, used to prevent internal short circuits and electrolyte mixing, while allowing ion transport. The quality and performance of the separator have a crucial impact on the safety, performance, and lifespan of the battery, therefore the production line of the separator is also a very important part of the lithium battery production line.
Process flow of lithium battery separator casting production line
The production line for lithium battery separator casting mainly includes process steps such as material preparation, coating, drying, calendering, forming, rolling, and coiling. The following will provide a detailed introduction to each stage:
Raw material preparation: The main raw materials for lithium battery separators include polypropylene (PP) film, conductive agents, plasticizers, and solvents. On the production line, it is necessary to prepare these raw materials and mix and stir them in a certain proportion to obtain a uniform mixture.
Film coating: Apply the mixed raw materials through a coating machine to form a uniform thin film. Coating machines usually use roll coating machines or solution immersion coating machines. By controlling the speed of the coating machine and the pressure of the coating head, films of different thicknesses and widths can be obtained.
Drying treatment: After coating, the film needs to be dried to remove solvents and moisture during the coating process. Usually, hot air circulation drying oven or infrared drying machine is used for drying treatment. By controlling the drying temperature and time, the film can reach the desired drying degree.
Polishing: The dried diaphragm material needs to undergo polishing treatment to improve the flatness and smoothness of the diaphragm. The calendering can be carried out using a calender machine, which applies pressure and temperature to the diaphragm material to achieve the desired calendering effect.
Forming and Rolling: The dried film needs to be formed and rolled to obtain the desired thickness and size. Forming is usually done by die-cutting or hot pressing, and the film is cut into the desired shape through a mold. Rolling is usually carried out using a roller press or a rolling mill. By controlling the pressure and speed of the roller press, the film can reach the desired thickness.
Pore treatment: Lithium battery separators need to have a certain pore structure to provide channels for ion transport. Pore treatment is usually carried out through heat treatment or chemical treatment. By controlling the temperature and time of the treatment, the film can have an appropriate pore structure.
Roll up: The diaphragm material that has undergone calendering treatment needs to be rolled up for subsequent cutting and packaging. The coiling is usually carried out using a coiling machine, which winds the diaphragm material into a roll shape for easy subsequent processing and use.
Testing and packaging: The lithium battery separator processed by the above process needs to undergo quality testing and packaging. Quality inspection usually includes testing of indicators such as thickness, porosity, pore size distribution, and resistivity to ensure that the performance of the diaphragm meets the requirements. Packaging is usually done by winding the membrane into a certain length of roll, and then packaging and labeling are carried out.
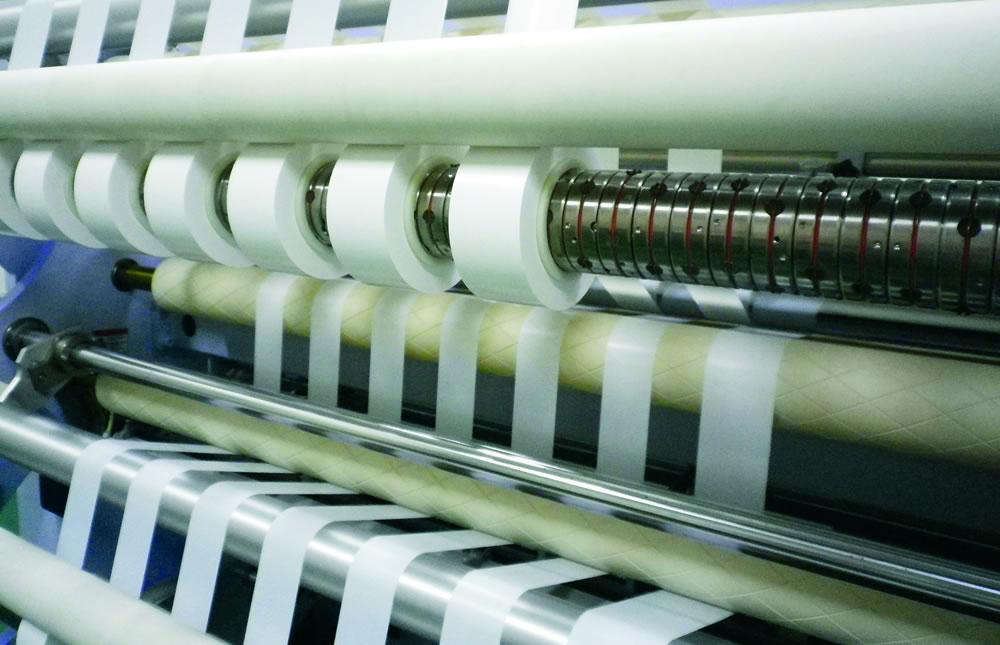
1.The main equipment of the lithium battery separator production line includes the following parts:
Material processing equipment: including material crushers, mixers, mixers, etc., used for processing and mixing raw materials.
Solution preparation equipment: including solvent tanks, mixing drums, heaters, etc., used to dissolve materials into a uniform solution.
Coating equipment: including coating machines, molds, etc., used to apply solutions onto membrane molds.
Curing equipment: including ovens, cooling machines, etc., used for curing the coated membrane.
Cutting equipment: including cutting machines, shaping machines, etc., used to cut and shape cured membranes to meet the required size and shape.
Packaging equipment: including packaging machines, sealing machines, etc., used to package cut diaphragms.
- Main technical parameters of lithium battery separator production line
The main technical parameters of the lithium battery separator production line include the following aspects:
Production line capacity: The production line capacity refers to the number of diaphragms that can be produced per hour or per day, generally measured in units of 10000 pieces per hour or 10000 pieces per day.
Diaphragm thickness: The thickness of a diaphragm refers to the thickness of the diaphragm, usually measured in micrometers.
Diaphragm width: The width of a diaphragm refers to the width of the diaphragm, usually measured in millimeters.
Diaphragm performance: The performance of the diaphragm includes conductivity, temperature resistance, chemical corrosion resistance, etc., which have a crucial impact on the performance and lifespan of the battery.
Production line investment: Production line investment refers to the total investment of the production line, including equipment procurement, factory construction, personnel training, and other expenses.
- Application areas of lithium battery separator production line
The application areas of lithium battery separator production lines mainly include the following aspects:
Electric vehicles: With the continuous popularity of electric vehicles, the demand for lithium battery separator production lines is also increasing, becoming an indispensable part of the electric vehicle industry chain.
Portable electronic devices: Lithium battery separators are also widely used in portable electronic devices such as mobile phones, tablets, laptops, etc.