River sand drying equipment is widely used in industries such as building materials, metallurgy, mineral processing, chemical engineering, and cement. It is mainly used for materials with high moisture content and significant proportion, such as slag, limestone, clay, river sand, etc
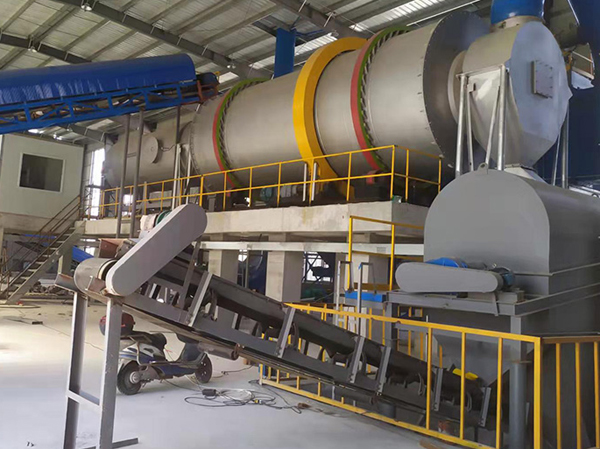
Manufacturer of river sand drying machine
The river sand drying production line mainly consists of a rotary drum, induced draft equipment, high-speed dispersing equipment, lifting plate, self-cleaning device, transmission device, conveying equipment, hot air equipment, reducer, support device, and sealing device. The complete set of river sand drying equipment has the advantages of reasonable design, excellent production, stable performance, advanced technology, high output, low energy consumption, small footprint, and high degree of mechanization.
Characteristics of River Sand Drying Production Line
1.Small footprint: reduces the footprint by about 60% compared to a single drum dryer. The investment in civil engineering has been reduced by about 60%.
2.Low energy consumption: Coal consumption is 1/3 of that of a single drum dryer, saving 40% of electricity, and consuming less than 9 kilograms of standard coal per ton.
3.High drying efficiency: Compared to traditional single drum dryers, it increases thermal efficiency by more than 40%.
4.Good drying effect: The initial moisture content of the material is 15%, and the final moisture content is ensured to be below 0.5-1%. It is the preferred equipment for bulk materials such as river sand, yellow sand, sea sand, pomegranate sand, etc.
Working principle of river sand drying production
The material enters the inner layer of the rotary drum through the feeding device, achieving downstream drying. The material continuously picks up and scatters under the inner layer’s plate, forming a spiral movement for heat exchange. The material moves to the other end of the inner layer and enters the middle layer for countercurrent drying. The material is continuously lifted back and forth in the middle layer, following a two-step forward and backward movement. The material not only fully absorbs the heat emitted by the inner drum, but also absorbs the heat from the middle drum, while extending the drying time. The material reaches a suitable drying state here. The material reaches the other end of the middle layer and falls into the outer layer. The material travels in a rectangular multi loop manner in the outer drum. The material that achieves the drying effect quickly travels out of the drum under the action of hot air. The wet material that does not achieve the drying effect cannot move quickly due to its own weight. The material is fully dried in this rectangular plate to achieve the drying purpose.
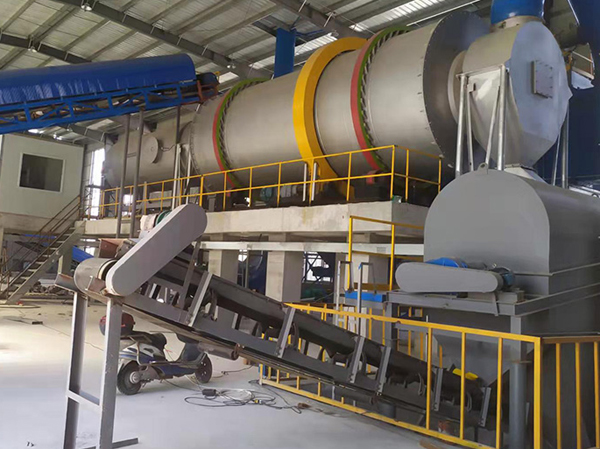
Structure of River Sand Drying Production Line
A three cylinder dryer is a method of shortening the external dimensions of a single cylinder dryer by replacing the single cylinder body with three cylinders stacked together. When the machine is in operation, the material and hot air flow enter the inner to outer cylinder in sequence. After the Z-shaped reciprocating flow of the body, the material is fully utilized to dry the material before being discharged.
The dryer cylinder is composed of three coaxial, horizontally placed inner, middle, and outer cylinder sleeves, which fully utilize the cross-section of the cylinder. The total length of its cylindrical shape is approximately 30-35% of that of a single cylinder. Thus significantly reducing the footprint and factory building area.
The supporting device of the machine is supported by the outer drum with a belt and a supporting wheel, which is directly driven by the motor. By friction between the supporting wheel and the tire belt, the cylinder rotates. The overall structure of the machine is compact, reasonable, and simple. In order to facilitate the maintenance and replacement of worn parts, it is designed as an axial split in the middle and connected by bolts.
Advantages of River Sand Drying Production Line
1.Compact structure, simple construction, reasonable layout, improve the heat exchange rate between materials and thermal energy, and achieve good drying effect of materials;
2.Less basic investment, only half of the same output of a single drum dryer, reduces one-time investment, occupies about 50% less land than a single drum dryer, reduces civil engineering investment by about 50%, and reduces electricity consumption by 60%;
3.Drying granular materials within a certain humidity and particle size range has a significant effect, such as yellow sand, molding sand, slag, coal slag, and small-sized clay;
4.Reliable operation, low energy consumption, high thermal efficiency, and fuel adaptability to coal, oil, and gas. Capable of drying block, granular, and powdered materials below 20mm.
5.The final moisture content can be easily adjusted according to user requirements.
6.Low exhaust temperature and long usage time of dust removal equipment.
7.No need for gear transmission, using idler transmission
Key points for selecting a river sand drying production line
1.Clear requirements: Before making a purchase, it is necessary to first clarify one’s production scale, material characteristics (such as humidity, particle size), drying requirements (such as temperature, time), etc., in order to choose the most suitable equipment model and configuration.
2.Inspecting manufacturers: Choosing manufacturers with production qualifications, technical strength, good reputation, and rich experience is the key to ensuring equipment quality and after-sales service. Suggest conducting on-site inspections of the manufacturer’s production line, sample displays, etc.
3.Performance testing: Before signing the purchase contract, the manufacturer is required to provide on-site testing or simulation testing opportunities to verify the actual drying effect, energy consumption indicators, and operational stability of the equipment.
4.Contract terms: The contract should specify the specific specifications, configuration, price, delivery time, after-sales service terms, etc. of the equipment to avoid disputes in the future.
5.Cost benefit analysis: Taking into account factors such as equipment investment, operating costs (such as energy consumption and maintenance expenses), and expected returns, conduct a cost-benefit analysis to ensure a return on investment.